Cura software provides a reliable method for calibrating a 3D printer’s extruder e-steps, which directly impacts print quality and accuracy. When users calibrate their extruder e-steps correctly, they can achieve precise filament extrusion rates and optimal print results. This comprehensive guide will walk them through the process of calibrating their extruder e-steps using Cura, helping them optimize their 3D printer’s performance and ensure consistent, high-quality prints every time.
Requirements and Prerequisites
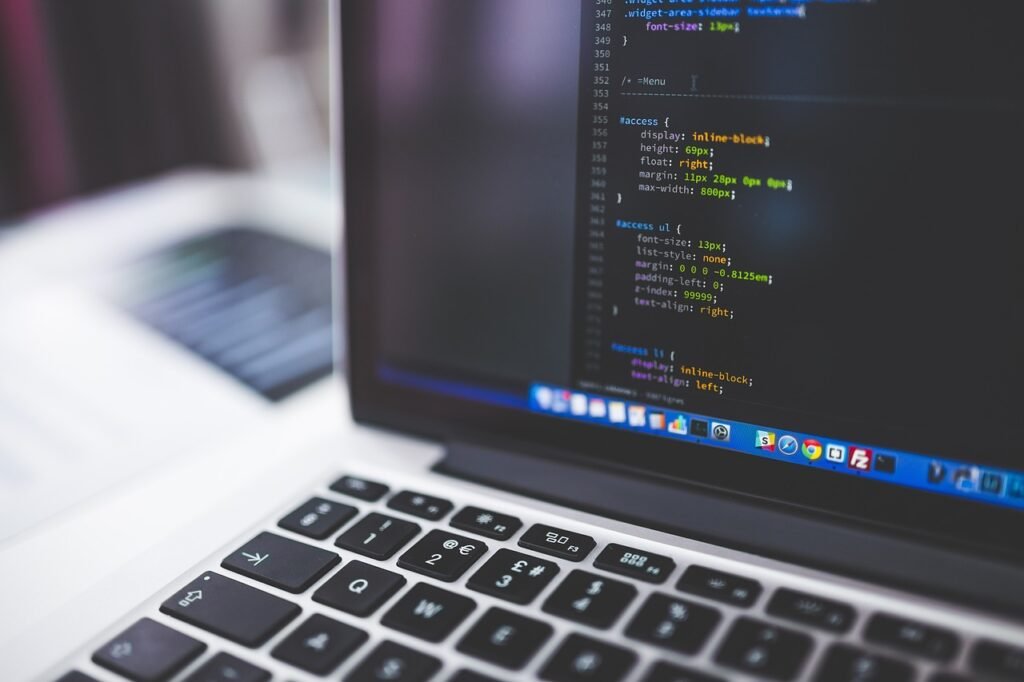
To successfully calibrate a 3D printer’s extruder e-steps using Cura, one needs specific tools, software, and safety measures in place. This comprehensive setup ensures accurate measurements and reliable results throughout the calibration process.
Essential Tools and Equipment
There’s a basic set of tools required for this calibration: digital calipers for precise measurements, a marker for marking filament, and clean filament for testing. Additional items include a small ruler or measuring tape, and basic maintenance tools for the extruder.
Software Requirements
You’ll need Ultimaker Cura (version 5.2.1 or later), a G-code terminal program, and potentially Notepad++ for editing configuration files. The printer’s firmware should be up-to-date to ensure compatibility with Cura.
Essential software components include proper printer profiles configured in Cura, updated firmware on the 3D printer, and any manufacturer-specific calibration utilities. These elements work together to ensure accurate e-steps calculations and implementations.
Safety Considerations
If working with heated components, users should exercise caution and follow proper safety protocols. This includes ensuring proper ventilation and wearing appropriate protective gear when handling hot extruder components.
It’s important to note that proper workspace organization and attention to safety procedures help prevent accidents and ensure accurate calibration results. Users should always refer to their printer’s manual for specific safety guidelines and maintain a clean, organized workspace throughout the calibration process. Here’s the requested content with specific formatting:
Understanding E-Steps Fundamentals
If a 3D printer is to produce accurate prints, proper calibration of the extruder steps per millimeter (E-steps) is vital. This fundamental setting determines how much the extruder motor turns to push a specific length of filament through the hot end, directly affecting print quality and dimensional accuracy.
What Are E-Steps and Their Importance
Little known to many beginners, E-steps represent the number of stepper motor steps required to extrude one millimeter of filament. This calibration setting ensures the printer delivers the exact amount of material needed, preventing issues like under-extrusion or over-extrusion that can compromise print quality.
Default Settings and Manufacturer Specifications
Little do most users realize that factory default E-steps settings are general estimates that may not be optimal for their specific printer setup. While manufacturers provide baseline values, variations in hardware, environmental conditions, and filament properties often necessitate customization.
Fundamentals of manufacturer specifications typically include default E-step values ranging from 90 to 100 steps/mm for direct drive extruders and 130 to 150 steps/mm for Bowden setups. These values serve as starting points but should be fine-tuned for optimal performance.
Signs of Incorrect E-Steps
On close inspection, prints with incorrect E-steps calibration show distinct characteristics. These may include gaps between layers, inconsistent extrusion patterns, or excess material buildup, all indicating the need for proper calibration.
What makes identifying incorrect E-steps crucial is their impact on print quality. Common indicators include stringing, under-filled layers, inconsistent line width, and dimensional inaccuracies. These issues can lead to structural weaknesses and poor surface finish in the final printed object. Here’s the requested content for the Pre-Calibration Setup section:
Pre-Calibration Setup
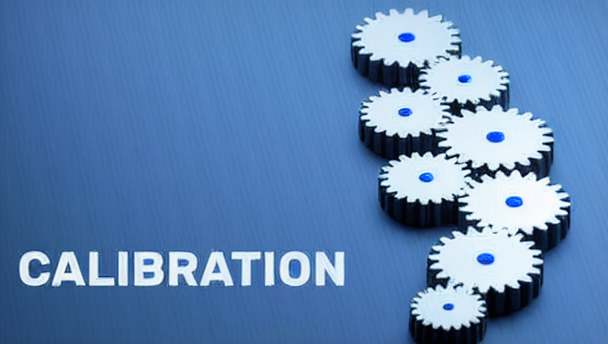
Not all 3D printers come perfectly configured from the factory, and e-steps calibration requires proper preparation. Before beginning the calibration process, users should ensure their printer is in optimal condition, the filament is properly prepared, and environmental factors are considered to achieve accurate results.
Printer Maintenance Check
On initial inspection, the printer should be examined for any mechanical issues. The extruder assembly should be clean, properly tensioned, and free from debris. The nozzle must be unclogged, and all moving parts should operate smoothly. This ensures accurate measurements during calibration.
Filament Preparation
With proper filament preparation being necessary, users should ensure their filament is dry, properly stored, and free from damage. The filament should be measured at room temperature and marked accurately for precise calibration.
PreCalibration of filament involves checking for consistent diameter throughout the length to be used, ensuring it’s free from moisture by proper storage or using a filament dryer, and examining for any physical defects that could affect extrusion accuracy.
Environmental Considerations
Little attention is often paid to environmental factors, but room temperature, humidity, and air circulation can significantly impact calibration accuracy. The calibration process should be performed in a controlled environment with stable conditions.
Maintenance of consistent environmental conditions throughout the calibration process is vital. Temperature fluctuations can affect filament properties, while high humidity can lead to moisture absorption. The ideal calibration environment maintains a temperature between 20-25°C and relative humidity below 50%. Here’s the requested content for the “Initial Measurements” section:
Initial Measurements
Many successful calibrations begin with accurate baseline measurements. This phase establishes the foundation for precise e-steps adjustment, ensuring optimal filament flow through the extruder. A methodical approach to initial measurements helps identify current extrusion issues and provides data for calculating necessary adjustments.
Current E-Steps Value Documentation
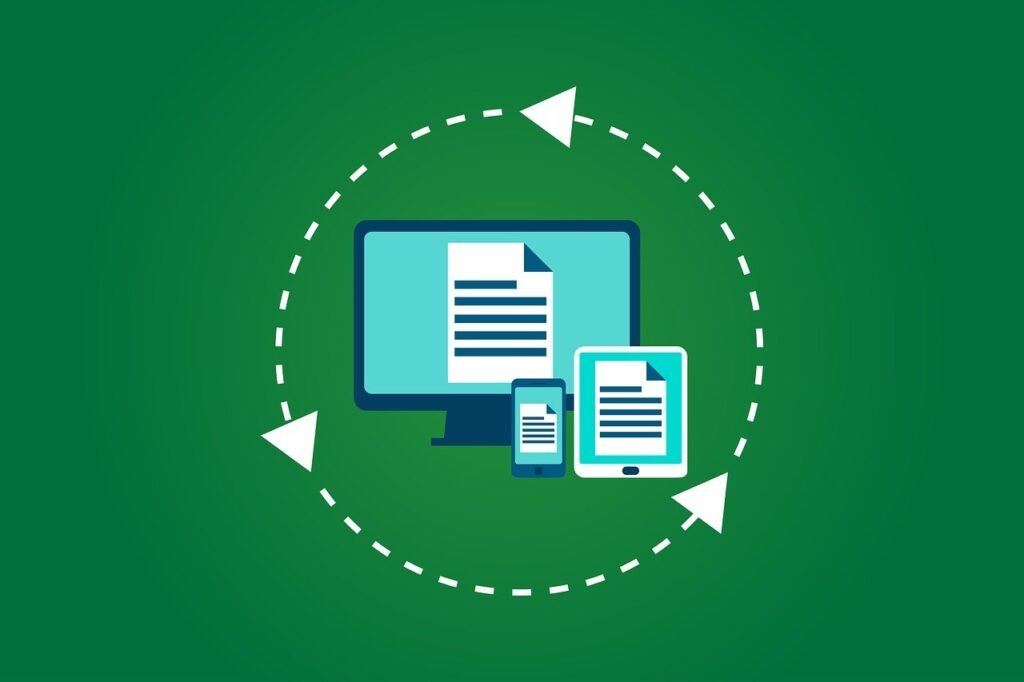
You need to locate and record the current e-steps value in your printer’s firmware settings. This value can typically be found through the LCD interface or by connecting to the printer via USB and sending an M503 command, which displays the current firmware settings including the e-steps value.
Filament Marking Procedure
You should measure and mark 120mm of filament from the entry point of the extruder using a ruler and permanent marker. This measurement serves as the starting point for calculating extrusion accuracy.
It’s crucial to make clear, precise marks on the filament at exactly 120mm from the extruder entry point. The marking should be thin enough to be visible but not so thick that it affects the filament’s movement through the extruder. Multiple measurements help ensure accuracy.
Reference Point Establishment
Filament position needs to be carefully noted relative to a fixed point on the extruder body. This reference point will be used to measure the actual amount of filament extruded during the calibration process.
This reference point serves as a consistent location for all measurements throughout the calibration process. The chosen point should be easily visible and remain unchanged during the entire procedure to maintain measurement accuracy. Here’s the requested content for the Cura Software Configuration section:
Cura Software Configuration
Your successful e-steps calibration starts with proper Cura software setup. The software needs to be configured correctly to communicate with the 3D printer and send the necessary commands for calibration. This section covers the necessary steps to set up Cura for e-steps calibration.
Accessing Machine Settings
Cura’s machine settings can be accessed through the Preferences menu by selecting “Printers” and then clicking on the active printer. These settings contain important parameters that need to be configured correctly for proper communication with the 3D printer.
Connection Setup
If the printer is being connected via USB, the correct port and baud rate must be selected in Cura’s connection settings. Most 3D printers operate at 115200 baud rate, but this may vary depending on the printer model.
The connection setup process involves selecting the appropriate COM port from the dropdown menu and ensuring the baud rate matches the printer’s specifications. Users should consult their printer’s manual for the correct settings if uncertain.
Terminal Commands Overview
An understanding of basic G-code commands is necessary for e-steps calibration. The terminal in Cura allows users to send these commands directly to the printer, enabling precise control over the calibration process.
To effectively use the terminal, users should familiarize themselves with common commands such as M92 (set steps per unit), M500 (save settings to EEPROM), and G1 (controlled move). These commands form the foundation of the calibration process. Here’s the requested content following your specifications:
Calibration Process
Once again, calibrating the extruder e-steps requires precision and attention to detail. The process involves measuring the current extrusion rate, calculating the necessary adjustments, and fine-tuning the settings until achieving optimal results. This systematic approach ensures accurate filament flow and improved print quality.
Extruder Temperature Settings
Filament Type | Temperature Range (°C) |
---|---|
PLA Filament | 190-210°C |
ABS Filament | 220-250°C |
PETG Filament | 230-250°C |
With proper temperature settings, the filament flows smoothly through the extruder, ensuring accurate measurements during calibration. The temperature should be adjusted according to the specific filament type being used.
Test Extrusion Procedure
Clearly, the test extrusion procedure requires marking 100mm of filament above the extruder entrance. The operator should ensure the filament moves freely without resistance during the test.
Process involves commanding the printer to extrude exactly 100mm of filament at a controlled speed of 100mm/min. During this step, it’s vital to monitor the filament movement for any irregularities or inconsistencies in extrusion speed.
Measurement Recording
The measurement recording phase involves carefully measuring the remaining filament length after the test extrusion. This measurement provides crucial data for calculating the new e-steps value.
This step requires measuring the distance between the original mark and the extruder entrance with digital calipers for maximum accuracy. The difference between the initial 100mm and the remaining length indicates whether the printer is over or under-extruding. Here’s the requested content for the “Calculations and Adjustments” chapter and its subsections:
Calculations and Adjustments
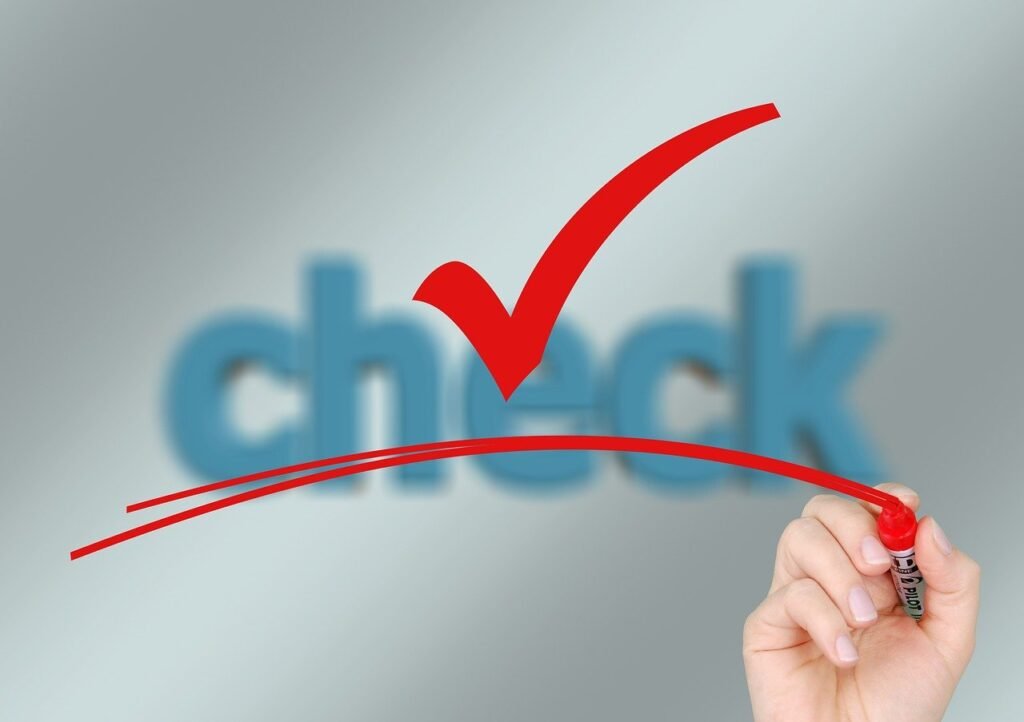
Keep the calibration process systematic by following precise mathematical calculations and making incremental adjustments. The process involves applying the e-steps formula, verifying results, and fine-tuning until optimal extrusion is achieved. A properly calibrated extruder typically requires 95-108 steps per millimeter, though this range can vary based on the printer model and filament type.
E-Steps Formula Application
Application of the e-steps formula follows a straightforward process: New E-steps = (Current E-steps × Expected Length) ÷ Actual Length. For example, if the current setting is 93 steps/mm and the printer extrudes 95mm instead of the commanded 100mm, the new value would be: (93 × 100) ÷ 95 = 97.89 steps/mm.
Value Verification Methods
ESteps verification requires multiple test extrusions to ensure consistency. After implementing new values, users should perform at least three test extrusions of 100mm each, measuring the actual output against the expected length. A variance of ±0.5mm is considered acceptable for most applications.
Methods for verification extend beyond basic measurements. Advanced users often employ digital calipers for precise measurements, while others use specialized testing protocols that include printing calibration cubes or thin-walled cylinders to verify extrusion accuracy under actual printing conditions.
Fine-Tuning Procedures
On completion of initial calculations, fine-tuning may be necessary to achieve optimal results. Users should make incremental adjustments of 1-2% to the e-steps value, testing after each modification until consistent extrusion is achieved. The final value should produce exact measurements across multiple test runs.
Formula refinement often requires consideration of material-specific factors. Temperature variations, filament diameter inconsistencies, and environmental conditions can all impact extrusion accuracy. Users should document their findings and maintain separate profiles for different filament types to ensure consistent results across various printing scenarios.
Implementation in Cura
Unlike manual calibration methods, Cura provides a streamlined interface for implementing e-steps adjustments. The software’s machine settings section allows users to modify extruder parameters directly, ensuring consistent application across all future prints. This approach eliminates the need for repetitive manual adjustments and provides a more reliable calibration process.
Updated Settings Input
On accessing the machine settings dialog in Cura, users can input the newly calculated e-steps value in the firmware settings section. This value, typically expressed in steps/mm, determines how many motor steps the extruder takes to push out one millimeter of filament. The software automatically validates the input to ensure it falls within acceptable parameters.
Configuration Saving
Assuming the new e-steps value has been entered correctly, users must save these changes to their printer’s configuration. This process involves clicking the “Save to EEPROM” button or adding the M500 command through the terminal interface.
Updated configurations are stored in the printer’s memory, ensuring the calibrated settings remain active even after power cycles. The software automatically applies these settings to all subsequent print jobs, maintaining consistent extrusion accuracy across different models and materials.
Backup Creation
Cura offers built-in functionality to create backups of printer configurations, including e-steps settings. This feature safeguards against accidental changes and provides a restoration point if needed. Users can export their settings to a file for future reference or troubleshooting.
Settings backups include all printer-specific configurations, including e-steps values, temperature profiles, and other calibration data. These backup files can be shared across different computers or restored if the software needs to be reinstalled, ensuring consistency in printer performance. Here’s the requested text for the Testing and Validation section:
Testing and Validation
After completing the initial calibration, it’s crucial to verify the accuracy of the new e-steps settings through comprehensive testing. This phase ensures that the calibration has successfully optimized the extruder’s performance and will produce consistent, high-quality prints.
Test Print Selection
Now is the time to choose appropriate test models that will effectively demonstrate the extruder’s calibration. A calibration cube, thin-walled cylinder, or benchmarking model like the #3DBenchy are ideal choices. These models feature various geometries that can reveal any remaining calibration issues.
Quality Assessment Methods
One of the most effective ways to evaluate print quality is through visual inspection and physical measurements. Key areas to examine include wall thickness, top surface quality, and layer consistency. A digital caliper can be used to measure the actual dimensions against the model’s specifications.
Understanding the relationship between e-steps calibration and print quality requires attention to specific indicators. Over-extrusion signs include bulging surfaces and excess material on edges, while under-extrusion manifests as gaps between layers or incomplete fills. Layer lines, corner quality, and surface finish also provide valuable feedback about calibration accuracy.
Results Documentation
Quality control requires careful documentation of test results. Recording initial settings, adjustments made, and final configurations helps track improvements and maintains consistency across future calibrations.
Methods for documentation should include photographs of test prints, measurements data, and notes about visual observations. Creating a calibration log with dates, filament types used, and environmental conditions can help identify patterns and troubleshoot issues in the future.
Advanced Calibration Techniques
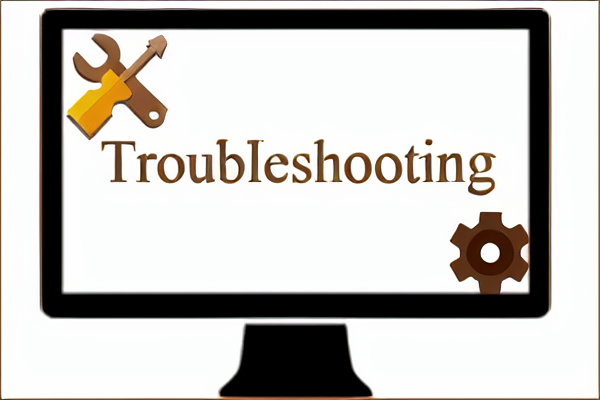
Now that the basic e-steps calibration is complete, advanced techniques can further optimize the printer’s performance. These methods ensure superior print quality across different materials and conditions.
- Multi-point verification process
- Temperature-based calibration adjustments
- Material-specific modifications
- Flow rate fine-tuning
Verification Points | Temperature Range | Flow Rate |
---|---|---|
20mm, 50mm, 100mm | 180°C – 260°C | 95% – 105% |
Multi-Point Verification
An vital step in advanced calibration involves testing extrusion at multiple distances to ensure consistency across different print lengths. This method helps identify any variations in extrusion rates that might occur during longer print jobs.
Temperature-Based Adjustments
With different printing temperatures affecting filament flow rates, calibration adjustments need to account for these variations.
Filament Type | Temperature Range |
---|---|
PLA | 180°C – 220°C |
PETG | 230°C – 250°C |
ABS | 220°C – 260°C |
For instance, higher temperatures can affect filament viscosity and flow characteristics, requiring specific e-steps adjustments.
Flow Rate Change | Retraction Adjustment |
---|---|
2-5% per 10°C | 0.5mm per 20°C |
Material-Specific Considerations
To achieve optimal results with different materials, calibration settings must be adjusted according to each filament type’s unique properties.
Understanding the relationship between material properties and e-steps calibration is vital for achieving consistent results across different filament types. Each material’s unique characteristics, such as density and thermal expansion, require specific adjustments to the e-steps values. Here’s the requested text for the Troubleshooting Guide chapter and its subsections:
Troubleshooting Guide
Despite following the calibration steps carefully, users may encounter various issues during the e-steps calibration process. Understanding common problems and their solutions can help achieve optimal results while minimizing frustration and wasted materials.
Common Error Patterns
For most users, typical issues include inconsistent extrusion rates, filament grinding, and irregular e-steps values. These patterns often manifest as under-extrusion (gaps in prints) or over-extrusion (excess material), with variations typically ranging between 5-15% from the target value.
Problem Resolution Steps
There’s a systematic approach to resolving e-steps calibration issues. First, verify the current e-steps value, then check for mechanical issues such as loose belts or worn gears, and finally ensure the extruder temperature is appropriate for the filament type being used.
A comprehensive resolution process involves documenting each adjustment and its results. Users should maintain a calibration log noting the initial e-steps value, subsequent adjustments, and corresponding print quality improvements. This methodical approach helps identify patterns and optimize the calibration process.
Verification Methods
If uncertainty exists about calibration accuracy, users should perform multiple test extrusions, measuring each result carefully. A minimum of three consecutive tests showing consistent results within 0.5mm variance indicates successful calibration.
Patterns in verification data provide valuable insights into calibration accuracy. Users should compare measurements across different print speeds and temperatures, ensuring consistent extrusion under various conditions. This comprehensive verification approach helps identify any remaining issues that might affect print quality. Here’s the requested content for the Maintenance Tips section:
Maintenance Tips
For optimal extruder performance and consistent e-steps calibration, regular maintenance is vital.
- Clean the extruder gear regularly to prevent filament debris buildup
- Check for wear on the extruder gear teeth
- Ensure proper tension on the extruder spring
- Inspect the PTFE tube for signs of wear
The frequency of maintenance depends on printing volume and material types used.
Regular Calibration Schedule
The recommended calibration frequency varies based on printer usage. For hobbyists printing 10-15 hours weekly, checking e-steps monthly is sufficient. Heavy users printing 40+ hours weekly should verify calibration bi-weekly. After changing filament types or brands, a quick calibration check ensures optimal performance.
Preventive Measures
Tips for maintaining accurate e-steps include storing filament properly, keeping the extruder assembly clean, and monitoring filament quality. Regular inspection of mechanical components helps prevent calibration drift and ensures consistent extrusion quality.
With proper preventive maintenance, users can significantly reduce the frequency of required calibrations. This includes keeping the printer in a controlled environment, using quality filaments, and maintaining proper lubrication of moving parts.
Performance Monitoring
Monitoring print quality through regular test prints helps identify potential e-steps drift early. Users should watch for signs of under or over-extrusion, such as gaps in layers or excessive stringing, which may indicate the need for recalibration.
For instance, maintaining a log of calibration values and corresponding print quality can help track performance over time. This data helps users identify patterns and predict when calibration might be needed, reducing troubleshooting time and improving overall print quality. Here’s the requested content for the Best Practices section:
Best Practices
Now that the basic calibration process is understood, implementing standardized practices ensures consistent results across multiple calibration sessions. Following established protocols, maintaining detailed records, and conducting regular quality checks can significantly improve the accuracy and reliability of e-steps calibration using Cura.
Documentation Methods
One effective approach to maintaining calibration accuracy is keeping detailed records of each calibration session. These records should include initial e-steps values, measurements taken, calculations performed, and final calibrated values. This documentation helps track changes over time and can be invaluable for troubleshooting future issues.
Quality Control Procedures
Control measures should be implemented at each stage of the calibration process. This includes verifying measurement accuracy, double-checking calculations, and conducting test prints to validate results. Regular calibration checks should be performed every 2-3 months or when changing filament types.
To ensure optimal results, implementing a systematic approach to quality control is important. This includes maintaining a clean working environment, using calibrated measuring tools, and following a standardized testing procedure for each calibration session. Regular verification of results helps maintain consistent print quality.
Workflow Optimization
Any successful calibration process requires an efficient workflow. Creating a checklist of steps, preparing all necessary tools beforehand, and following a systematic approach can significantly reduce calibration time while maintaining accuracy.
Workflow optimization can be achieved through careful planning and organization. This includes setting up a dedicated calibration station, maintaining a clean workspace, and having all necessary tools readily available. A well-organized workflow can reduce calibration time by up to 50% while ensuring consistent results.
Read our Latest Blogs & Product reviews on 3D Printing
Summing up
Taking this into account, anyone looking to calibrate their 3D printer’s extruder e-steps using Cura should follow a systematic approach. They should start by gathering the necessary tools, accurately measuring the filament extrusion, and calculating the correct e-steps using the provided formula. Once they have determined the optimal settings, they can update their machine configuration in Cura and validate the results through test prints. This process ensures that their 3D printer consistently delivers precise filament extrusion, leading to higher quality prints and improved overall performance.