You may be wondering if it’s possible for a 3D printer to create items out of rubber material. In this informative blog post, we will explore the technology behind 3D printing and research into whether or not these machines can print with rubber. By the end of this article, you will have a clearer understanding of the capabilities of 3D printers when it comes to working with rubber-like materials.
Key Takeaways
- Flexible filaments: 3D printers can print rubber-like materials using flexible filaments that mimic the properties of rubber. These flexible filaments can create objects with the desired flexibility and elasticity.
- Support structure: Printing rubber materials may require a support structure to prevent the object from deforming during printing. Specialized 3D printers or modifications may be needed to print rubber efficiently.
- Applications: Rubber-like 3D printing is useful for creating prototypes, custom designs, and functional parts that require flexibility, such as gaskets, seals, and prosthetics.
The Basics of 3D Printing
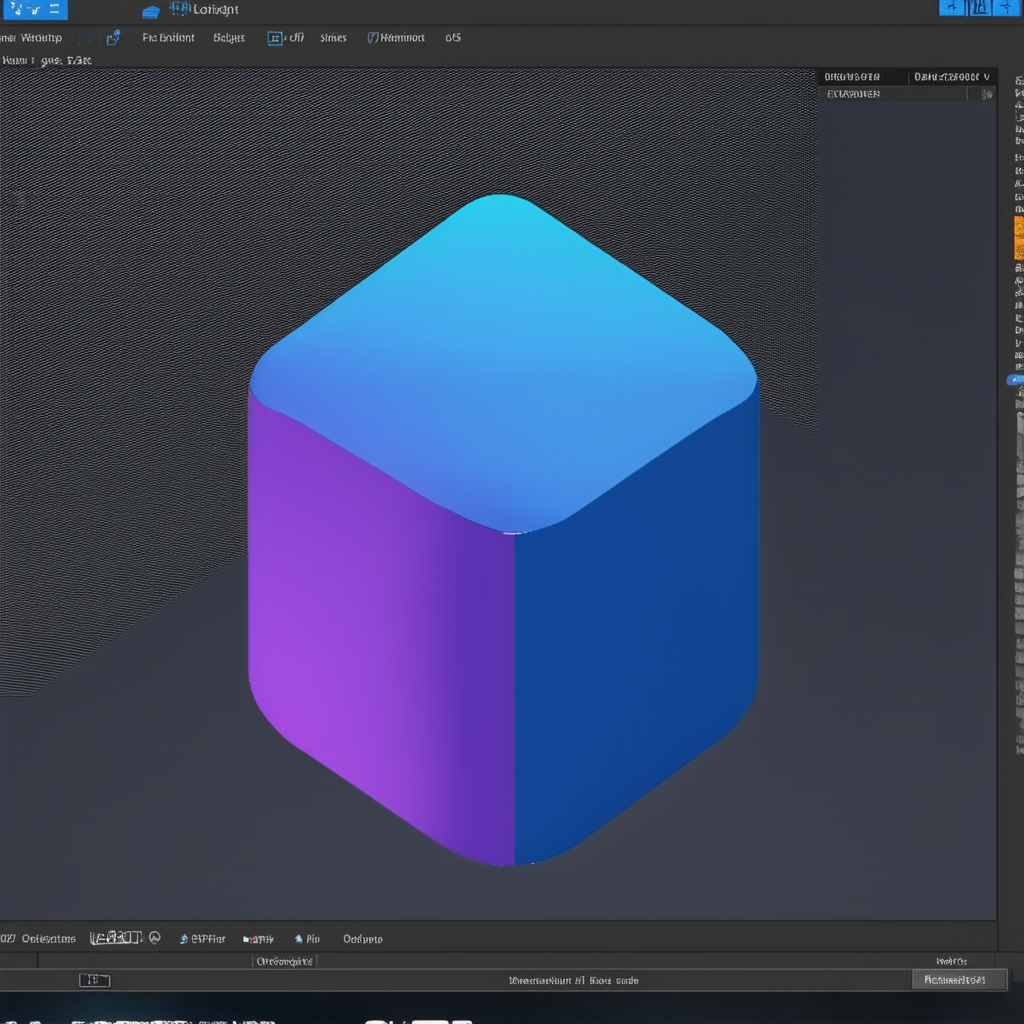
While 3D printing may seem like a complex process, it is actually quite simple once you understand the basics. Additive manufacturing, as it is also known, involves creating a three-dimensional object by adding material layer by layer. This is in contrast to traditional subtractive manufacturing processes, where material is cut away to create the final product.
Additive Manufacturing Process
Additive manufacturing process begins with creating a digital design of the object you want to print. This design is then sliced into thin horizontal cross-sections by the 3D printer software. The printer then follows these slices, layering material on top of each other until the entire object is created. This layer-by-layer approach gives 3D printing its precision and versatility in creating complex geometries.
Rubber Properties and Challenges
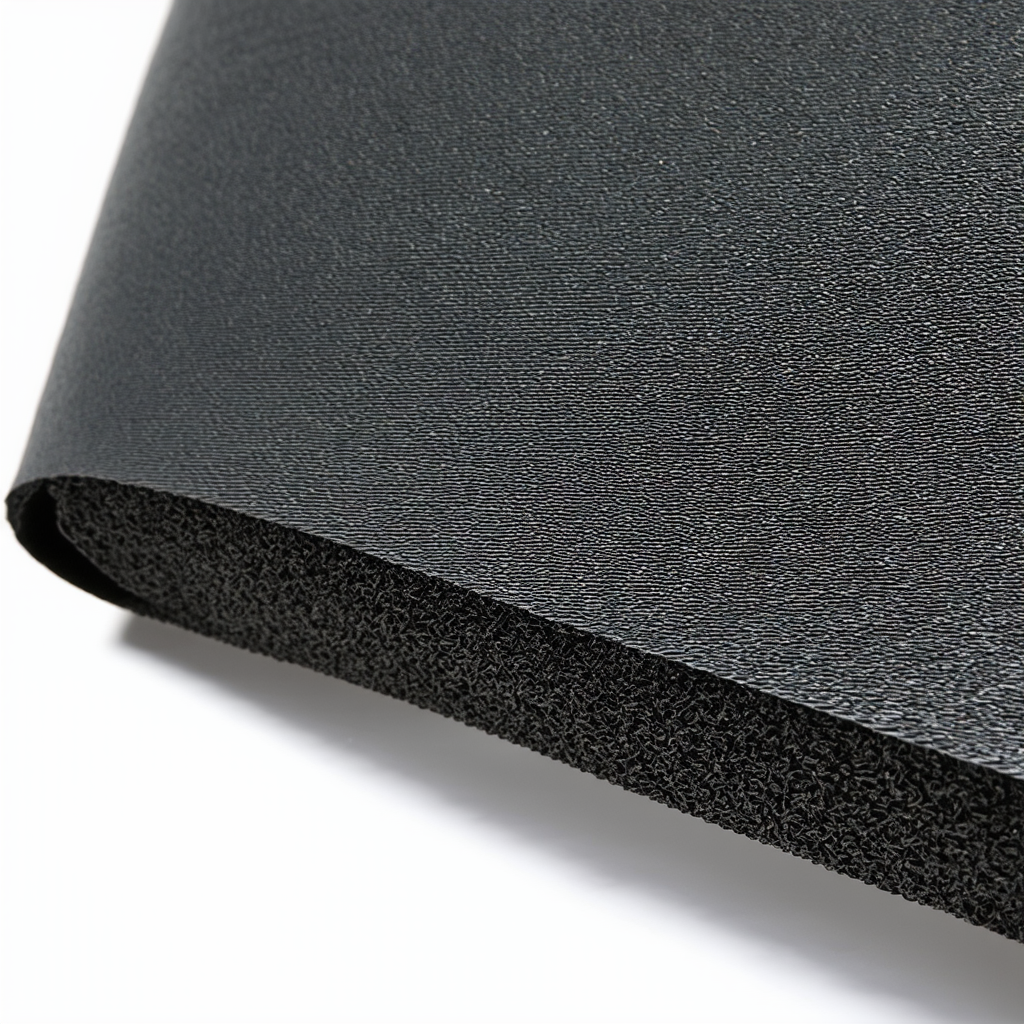
Elasticity and Flexibility
One of the key properties of rubber is its elasticity, which allows it to deform under stress and return to its original shape when the stress is removed. This property makes rubber ideal for applications where flexibility is crucial, such as in seals, gaskets, and shock absorbers. When considering 3D printing rubber-like materials, it is crucial to ensure that the material can retain its elasticity after the printing process. The challenge lies in finding a 3D printing technique that can accurately replicate the intricate structure of rubber while maintaining its flexibility.
Thermal Resistance and Conductivity
Challenges in 3D printing rubber-like materials also extend to thermal resistance and conductivity. Rubber is known for its heat resistance and low thermal conductivity, making it a suitable choice for applications where temperature variations are common. 3D printing rubber with these properties can be tricky, as maintaining the material’s thermal characteristics during the printing process can be challenging. Additionally, ensuring that the printed rubber retains its thermal resistance and conductivity post-printing is a significant hurdle that needs to be addressed.
With advancements in 3D printing technology, researchers and engineers are exploring new materials and printing techniques to overcome these challenges and create rubber-like materials that exhibit the desired thermal properties.
Chemical Resistance and Reactivity
The chemical resistance of rubber is another vital property that makes it suitable for various industrial applications. Rubber is often used in environments where it may come into contact with chemicals or harsh substances, requiring it to resist degradation and maintain its structural integrity. When attempting to 3D print rubber-like materials, it is crucial to ensure that the printed material retains its chemical resistance and reactivity similar to traditional rubber.
A thorough understanding of the interactions between the printing material, the printing process, and the post-processing steps is crucial in developing rubber-like materials with the desired chemical properties.
Current State of Rubber 3D Printing
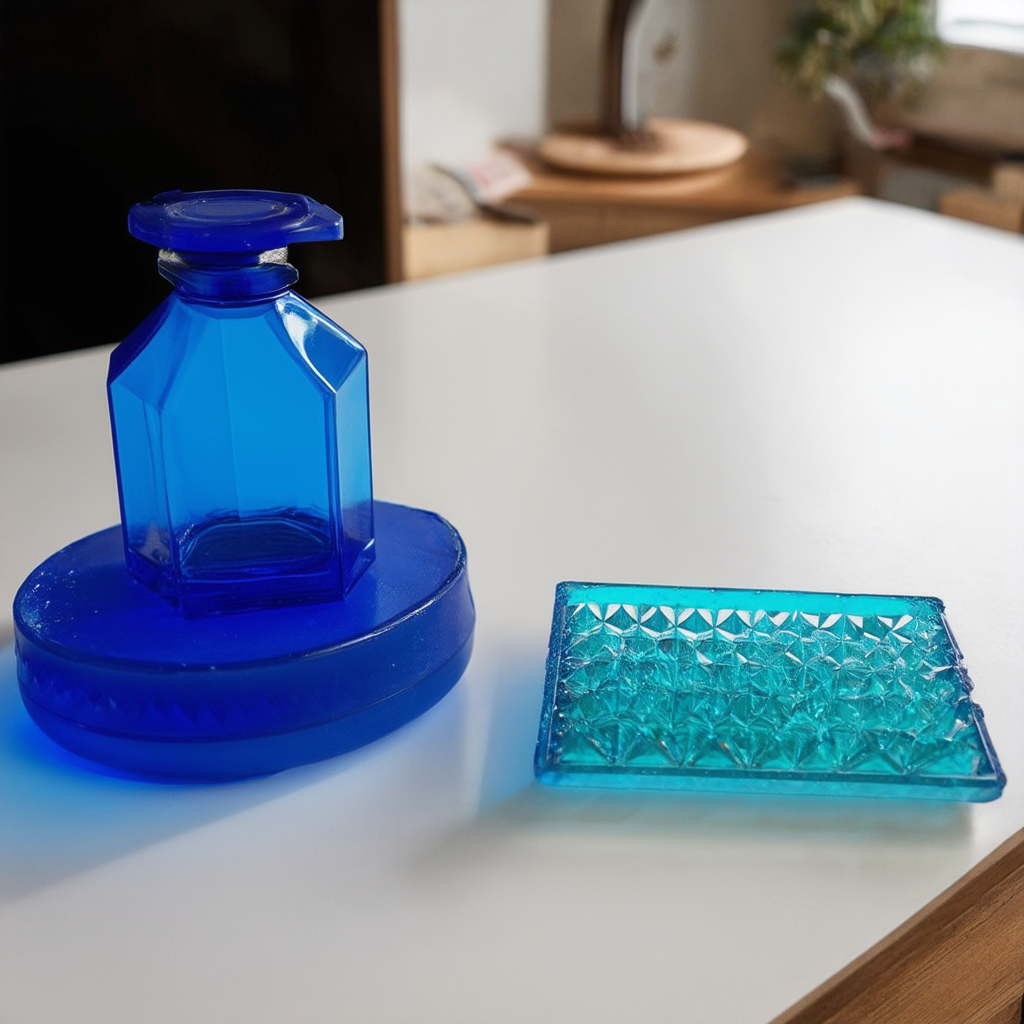
FDM/FFF Limitations
State-of-the-art FDM/FFF 3D printers have limitations when it comes to printing rubber-like materials. The traditional thermoplastic filaments used in these printers are rigid and lack the flexibility and elasticity required for rubber-like prints. As a result, achieving true rubber-like properties with FDM/FFF technology remains a challenge.
SLA/DLP/Polyjet Possibilities
With SLA, DLP, and Polyjet technologies, there are more possibilities for printing rubber-like materials. These resin-based printers can produce parts with higher detail and smoother surfaces, allowing for the creation of objects that mimic the properties of rubber more closely. By using specialized rubber-like resins, you can achieve prints with increased flexibility and elasticity, making them suitable for a wider range of applications.
Additionally, SLA/DLP/Polyjet printers can incorporate support structures that are easier to remove, resulting in cleaner finishes for your rubber-like prints. This makes these technologies particularly useful for creating intricate designs that require a high level of accuracy and smoothness.
SLS/SLM/DMLS Opportunities
Plus, SLS, SLM, and DMLS technologies offer even more opportunities for printing rubber-like materials. These powder-based systems allow for the use of a wider range of materials, including flexible and elastomeric powders that can produce parts with properties similar to rubber. By using these advanced 3D printing methods, you can create objects with increased durability and resilience, making them ideal for applications where flexibility is key.
The versatility of SLS, SLM, and DMLS printers also enables you to experiment with different rubber-like materials to achieve the desired level of softness, hardness, and elasticity in your prints. This gives you greater control over the mechanical properties of your objects, allowing you to tailor them to specific requirements.
Printing rubber-like materials with 3D printers is an exciting area of exploration, with each technology offering unique possibilities and advantages. Depending on your specific needs and the properties you want your prints to exhibit, you can choose the best 3D printing method to bring your rubber-like creations to life.
Alternative Materials and Solutions
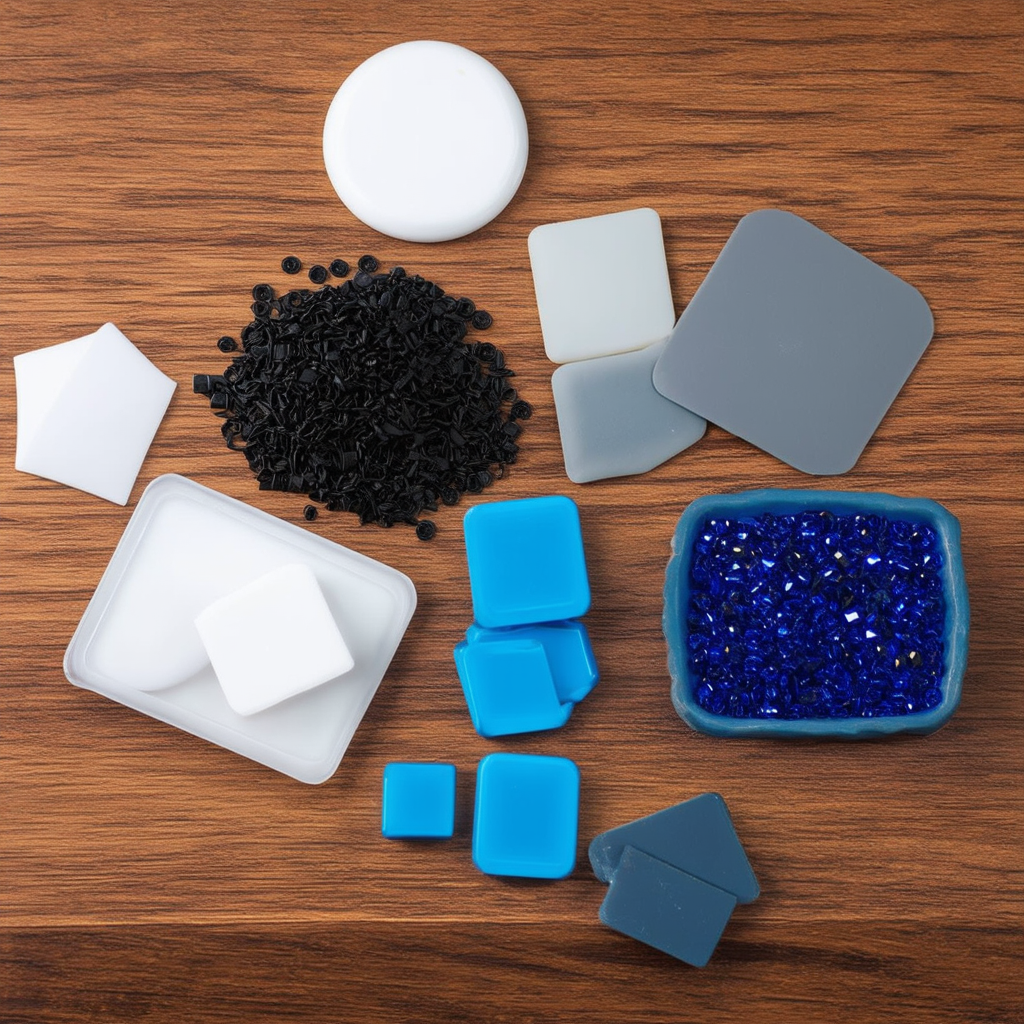
Thermoplastic Elastomers (TPE)
Despite the limitations of printing rubber directly with a 3D printer, there are alternative materials that can provide similar flexibility and elasticity. One such option is Thermoplastic Elastomers (TPE), which are a class of materials that combine the characteristics of thermoplastics and elastomers. These materials are known for their resilience and can be used to create objects with rubber-like properties.
Materials such as TPE can be utilized in 3D printing to produce parts that require elasticity and durability. While not technically rubber, TPE is a suitable substitute that can be used for a variety of applications where traditional rubber would be used.
Silicone-based Materials
For those looking to print objects with a softer, more rubbery feel, silicone-based materials offer a viable solution. These materials are known for their flexibility, heat resistance, and biocompatibility, making them ideal for creating rubber-like products through additive manufacturing.
For instance, you can use silicone-based materials to print items such as custom seals, soft grips for tools, or even prosthetic components that require a softer touch. These materials are versatile and can help you achieve the desired rubber-like properties in your 3D-printed objects.
Hybrid Materials and Composites
On the frontier of 3D printing technology are hybrid materials and composites that combine rubber-like properties with other materials to achieve specific characteristics. By blending rubber-like materials with more rigid substances, you can create products that exhibit the best of both worlds—flexibility and strength.
Materials such as these can be tailored to meet the requirements of your specific application, whether you need a part that is tough yet flexible or one that can withstand repeated stress while maintaining its shape. The possibilities with hybrid materials and composites are expanding the potential of 3D printing, allowing for the creation of complex, functional objects with unique material properties.
Research and Development Efforts
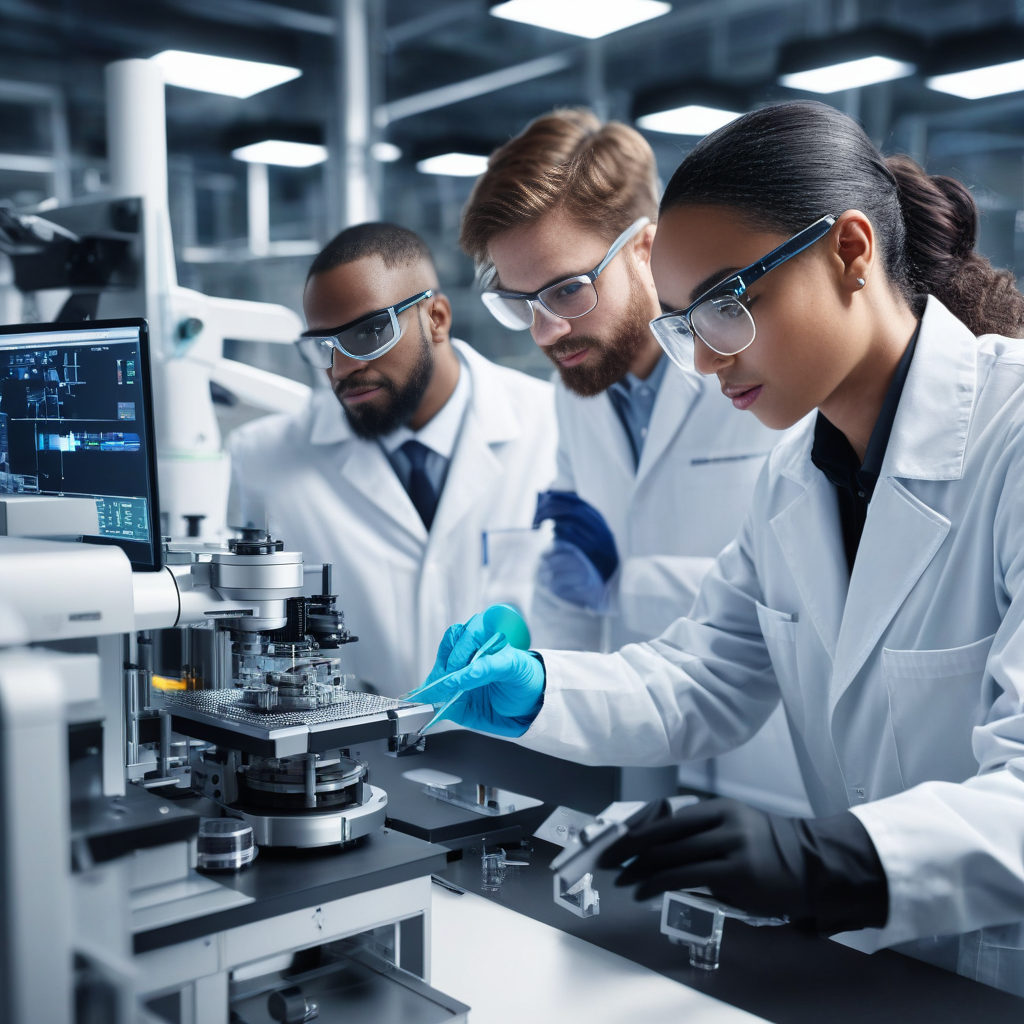
Not surprisingly, researchers and industry experts have been exploring the possibilities of 3D printing rubber-like materials. The flexibility and resilience of rubber make it a valuable material in numerous applications, from prototyping to manufacturing custom products.
Academic and Industrial Initiatives
Research in academia and industry has been focused on developing new formulations that can be 3D printed to mimic the properties of rubber. These efforts aim to create materials that have the elasticity and durability required for various practical uses. Collaborations between material scientists, engineers, and manufacturers have been instrumental in advancing this technology.
New Materials and Technologies
On the frontier of 3D printing rubber-like materials are innovative techniques such as multi-material printing, which allows for the fabrication of objects with varying levels of hardness and flexibility. By combining different polymers and additives, researchers can tailor the properties of the printed material to closely resemble those of natural rubber.
For instance, some recent studies have shown promising results in using a combination of thermoplastic polyurethane (TPU) and other elastomers to create 3D printed objects with rubber-like characteristics. These advancements have opened up new possibilities for printing flexible components and functional prototypes.
Overcoming Current Limitations
Overcoming the challenges associated with 3D printing rubber has been a key focus for researchers. Issues such as print resolution, layer adhesion, and material consistency have presented obstacles in achieving high-quality rubber-like prints. However, advancements in printer technology and material development are steadily addressing these limitations.
Another area of exploration is post-processing techniques that can enhance the mechanical properties of 3D printed rubber-like materials. By optimizing curing processes and surface treatments, researchers are working towards improving the strength and durability of printed objects.
Applications and Potential Uses
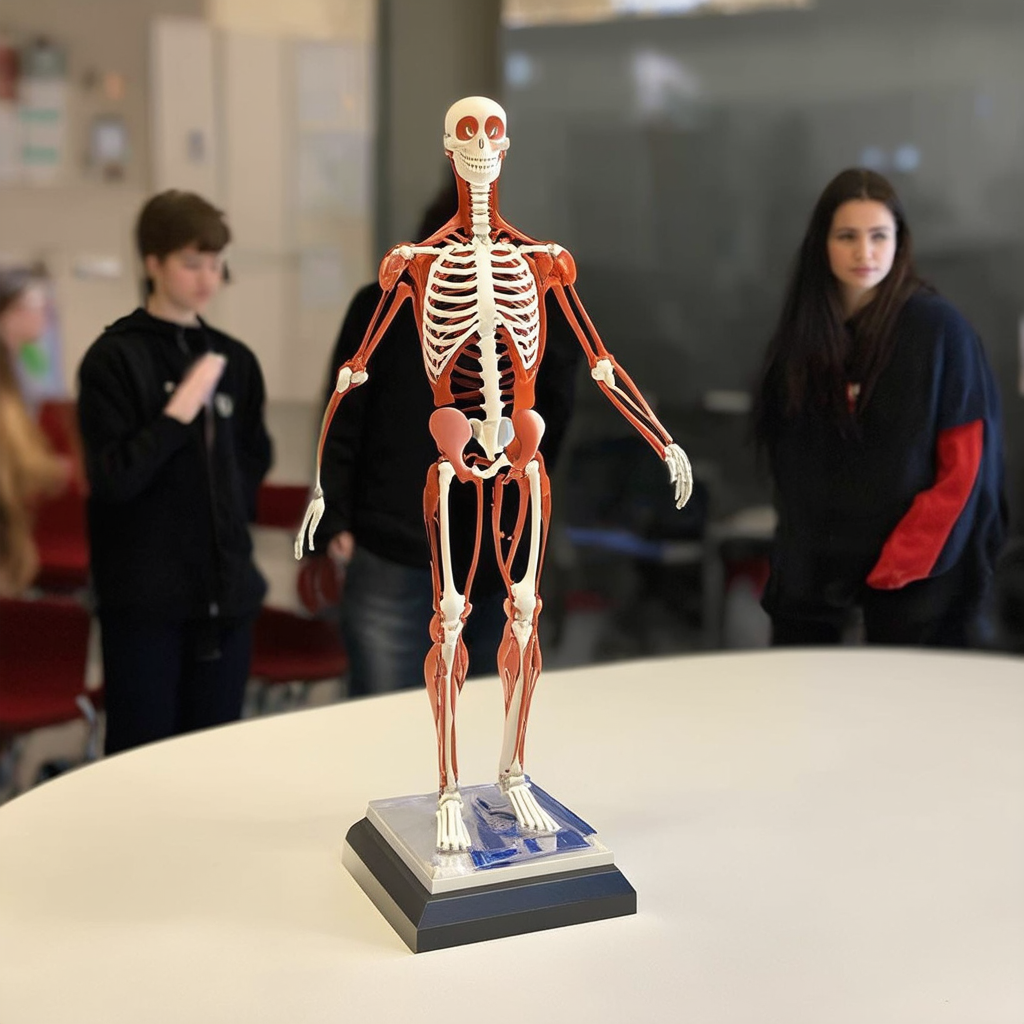
Industrial and Commercial Applications
Many industrial and commercial sectors can benefit from 3D printing rubber. To start, in industries where custom seals, gaskets, or grips are required, a 3D printer can provide a cost-effective solution for producing these items quickly and efficiently. Manufacturers can also use 3D printing to create prototype parts for testing before mass production. Furthermore, the flexibility of rubber-like materials opens up possibilities for producing intricate designs and complex geometries that may be challenging with traditional manufacturing methods.
Medical and Biomedical Applications
Biomedical professionals are increasingly turning to 3D printing to create patient-specific medical devices, prosthetics, and anatomical models. With the ability to print soft and flexible materials like rubber, medical practitioners can develop custom-fitted splints, orthotics, and even surgical tools that conform precisely to a patient’s anatomy. This level of personalization can lead to improved treatment outcomes and patient comfort.
Biomedical applications of 3D printing are revolutionizing the healthcare industry. From creating lifelike organ models for surgical planning to producing bio-compatible implants, the potential for utilizing rubber-like materials in medical settings is vast. Researchers are continuously exploring new ways to harness the capabilities of 3D printing to advance patient care and medical innovation.
Consumer and Recreational Applications
Uses for 3D printed rubber extend beyond industrial and medical fields. Potential applications in consumer goods include custom smartphone cases, ergonomic handles for tools, and protective covers for electronic devices. Additionally, in recreational activities, 3D printed rubber components can enhance sporting equipment, gaming accessories, and hobbyist projects. The ability to tailor the properties of rubber materials through 3D printing gives individuals the freedom to create personalized products that suit their specific needs and preferences.
Potential consumer and recreational applications of 3D printed rubber present exciting opportunities for hobbyists, designers, and enthusiasts alike. Whether you are looking to customize your gadgets, improve your sports gear, or bring your creative ideas to life, 3D printing with rubber-like materials offers endless possibilities for innovation and self-expression.
Conclusion
Presently, you have learned that 3D printers can print rubber-like materials using a special filament called TPU or flexible resin. While traditional rubber materials like silicone are challenging to print due to their flexible and elastic properties, advancements in 3D printing technology have made it possible to create objects with rubber-like qualities. This opens up new possibilities for creating custom designs, prototypes, and functional objects that require flexibility and durability.
Whether you are a designer, engineer, artist, or hobbyist, experimenting with 3D printing rubber materials can bring your creations to life in ways that were previously challenging. By understanding the capabilities of 3D printers and the different types of rubber-like filaments available, you can unleash your creativity and push the boundaries of what is possible in the world of additive manufacturing.
Q: Can a 3D printer print Rubber?
A: Yes, certain 3D printers have the capability to print rubber-like materials known as TPE (Thermoplastic Elastomer) or TPU (Thermoplastic Polyurethane).
Q: What are the characteristics of rubber-like materials used in 3D printing?
A: Rubber-like materials used in 3D printing are flexible, durable, and have good impact resistance. They can be used to create prototypes, cosplay props, custom phone cases, and other products that require a soft and rubbery texture.
Q: How do I 3D print with rubber-like materials?
A: To 3D print with rubber-like materials, you will need a 3D printer that supports flexible filaments such as TPE or TPU. Make sure your printer’s extruder is capable of handling flexible materials to prevent jamming. Adjust your printer settings such as print speed, temperature, and retraction settings to achieve good results when printing with rubber-like materials.