Over the years, 3D printing technology has advanced in remarkable ways, but when it comes to printing silicon, things get a bit more complicated. To answer the question, “Can a 3D printer print Silicon?” let’s research into the intricacies of silicon’s properties and the challenges involved in using 3D printers for this task. By the end of this article, you will have a clearer understanding of the possibilities and limitations when it comes to printing silicon with a 3D printer.
Key Takeaways
- Silicon printing is challenging: 3D printers struggle with printing silicon due to its high melting point, limited printability, and the need for precise control during the printing process.
- Silicon inks and alternative methods: Researchers are developing silicon inks and alternative methods, such as stereolithography and binder jetting, to enable 3D printing of silicon-based materials.
- Potential applications: If successful, 3D printing of silicon could revolutionize electronic and medical device manufacturing, enabling custom-made and intricate designs that are currently difficult to produce using traditional methods.
The Basics of 3D Printing
How 3D printing works
While 3D printing might seem like a futuristic concept, its basic principle is quite simple. On a fundamental level, 3D printing works by creating a three-dimensional object layer by layer. It’s similar to how you might stack multiple slices of bread to make a sandwich, but in this case, each slice represents a thin layer of material that is gradually built up to form the final object.
The Properties of Silicon
What is silicon?
The element silicon is a chemical element with the symbol Si and atomic number 14 on the periodic table. It is a hard, brittle crystalline solid with a blue-grey metallic luster. Silicon is the second most abundant element in the Earth’s crust after oxygen, making up about 27.7% of the crust by mass.
Physical and chemical properties of silicon
Silicon has some unique properties that make it an necessary element in various industries, including electronics and solar energy. It is a semiconductor, meaning it can conduct electricity under some conditions but not others, making it a crucial component in the production of computer chips and solar cells. Silicon has a high melting point of 1414°C and a boiling point of 3265°C, making it stable at high temperatures.
Understanding the physical and chemical properties of silicon is crucial in the fields of materials science and engineering, as it plays a significant role in the development of new technologies and applications. Silicon’s ability to form bonds with other elements allows for the creation of various silicon-based materials with unique properties tailored for specific uses.
Challenges of Printing Silicon
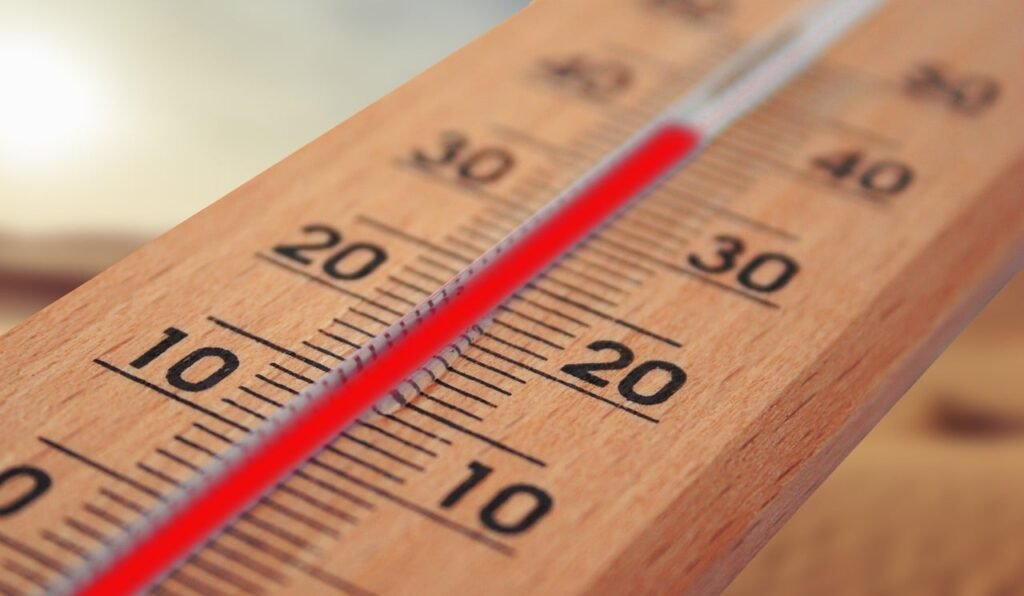
Why silicon is difficult to print
One of the main reasons why printing silicon is challenging is because of its high melting point of 1414°C (2577°F). This is significantly higher than the melting points of most materials commonly used in 3D printers, such as plastics or metals. Achieving and maintaining such high temperatures consistently throughout the printing process presents a major technical challenge.
Temperature and melting point considerations
Temperature | Melting Point |
Ambient | 1414°C (2577°F) |
To print silicon successfully, you would need a 3D printer capable of reaching and sustaining temperatures well beyond those of conventional 3D printers. This demands advanced heating elements and temperature control systems to prevent the silicon from solidifying prematurely.
Understanding Reactivity and contamination concerns
Silicon is highly reactive with many elements and compounds, making it challenging to work with while maintaining its purity level. Contamination can easily occur during the printing process, affecting the material’s properties and resulting in subpar printed objects.
For instance, if silicon comes into contact with oxygen during the printing process, it can form silicon dioxide, a common contaminant. This can degrade the material’s quality, affecting its mechanical and electrical properties.
Current State of Silicon 3D Printing
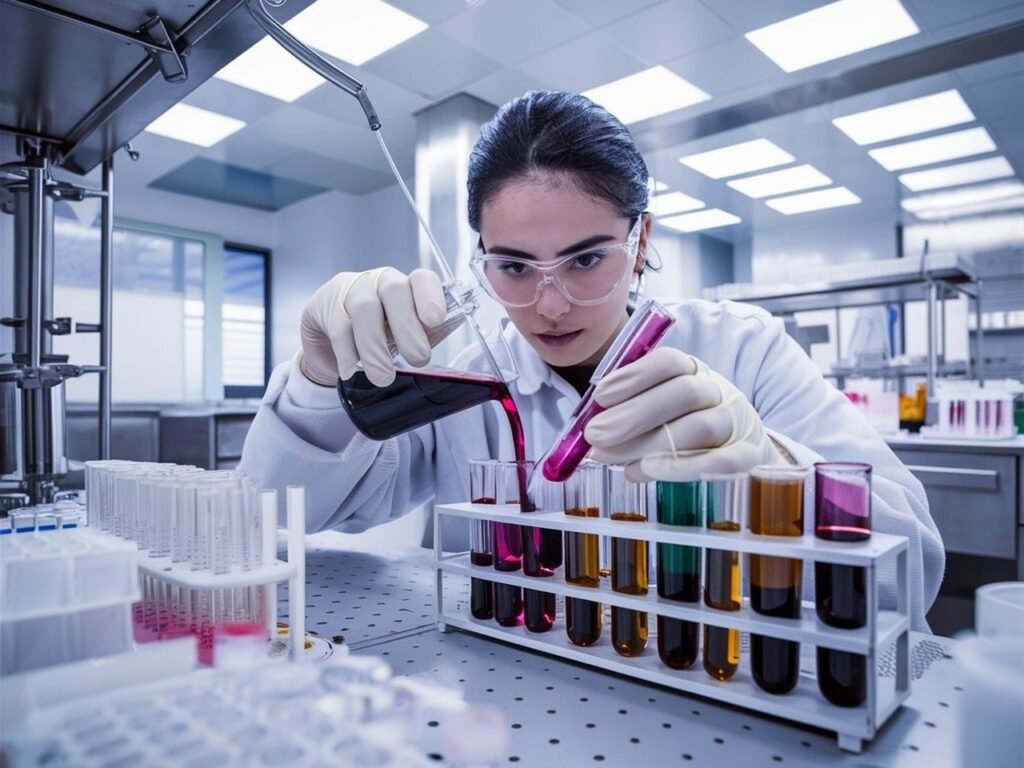
Despite the remarkable advancements in 3D printing technology, printing with silicon remains a significant challenge. Silicon is a complex material with unique properties that make it difficult to work with using traditional 3D printing methods.
Research and development efforts
Efforts to develop 3D printing methods specifically for silicon are ongoing, with researchers exploring various techniques to effectively print silicon structures. Scientists are investigating new materials, processes, and machines that can handle the challenges presented by silicon printing.
Current methods and techniques
One of the primary methods for printing with silicon involves using high-temperature processes in a controlled environment to deposit silicon layer by layer. This technique requires specialized equipment and precise conditions to ensure the silicon retains its desired properties during the printing process.
Limitations and obstacles
Obstacles in silicon 3D printing include the material’s high melting point, which makes it challenging to work with using traditional 3D printers designed for plastics. Additionally, achieving high-resolution prints with silicon is difficult due to its tendency to crack or warp during the printing process.
The development of silicon 3D printing technology is still in its early stages, and researchers are actively working to overcome these limitations to unlock the full potential of printing with silicon.
Potential Applications of Silicon 3D Printing
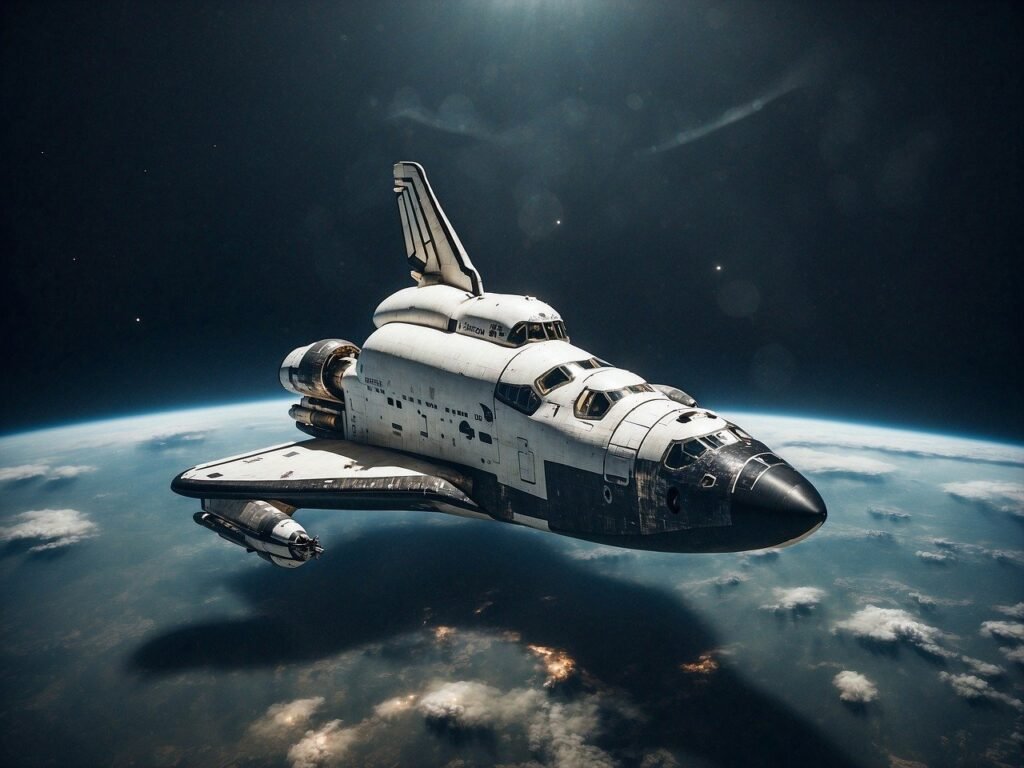
Electronics and Semiconductors
Printing silicon opens up a world of possibilities in the electronics and semiconductor industries. You can now create intricate and custom-designed silicon components that are vital for the functioning of various electronic devices. With 3D printing, you have the flexibility to print complex structures and circuits that were previously impossible to achieve with traditional manufacturing methods.
Imagine being able to print customized silicon chips for your electronic devices, tailored to your specific needs. This level of customization and precision can revolutionize the way electronic components are produced, leading to more efficient and powerful devices in your hands.
Aerospace and Defense
For aerospace and defense applications, the ability to print silicon components can significantly enhance the performance and reliability of critical systems. You can now design and manufacture lightweight but incredibly durable silicon parts that are vital for aircraft, satellites, and military equipment.
To demonstrate, imagine printing complex silicon components for a satellite that can withstand extreme temperatures and harsh conditions in space. With 3D printing technology, you have the capability to create intricate structures that can improve the overall efficiency and longevity of aerospace and defense systems.
Biomedical and Healthcare
One promising area for silicon 3D printing is in the field of biomedical and healthcare applications. You can now create custom-made silicon implants and medical devices that perfectly fit the unique anatomies of individual patients. This personalized approach can significantly improve patient outcomes and reduce the risk of rejection or complications.
It’s also possible to print microfluidic devices and lab-on-a-chip systems using silicon, enabling precise drug delivery systems and advanced diagnostic tools. The versatility of silicon 3D printing in the biomedical field is truly groundbreaking and has the potential to transform healthcare as you know it.
Alternatives to Direct Silicon Printing
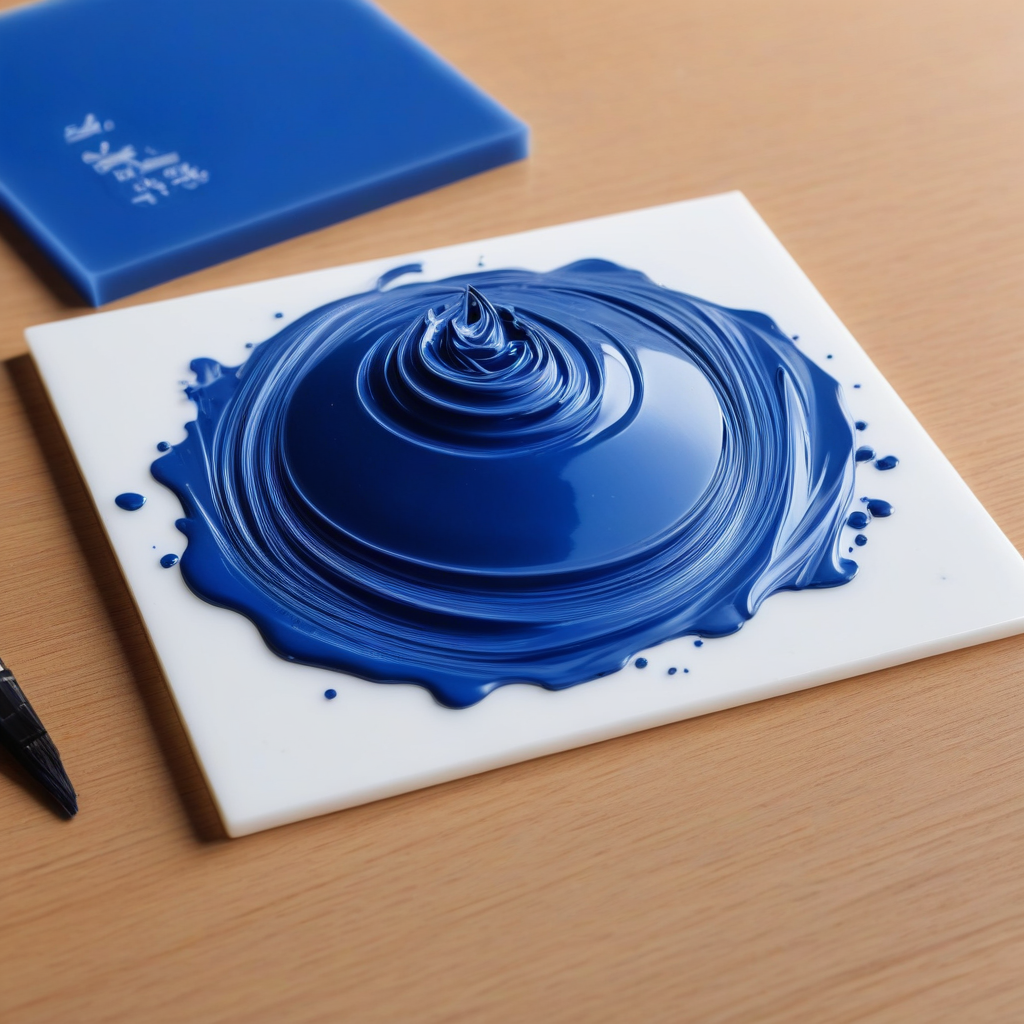
Printing silicon-based materials
Alternatives to directly printing silicon involve using silicon-based materials that can be printed with conventional 3D printers. These materials are designed to mimic the properties of silicon, offering a feasible option for creating silicon-like structures without the need for specialized equipment.
Using silicon-based inks and pastes
When considering alternatives to directly printing silicon, using silicon-based inks and pastes is a viable option. These materials contain a high concentration of silicon particles suspended in a liquid medium, allowing for precise deposition and formation of silicon-based structures.
Plus, silicon-based inks and pastes can be optimized for specific applications, offering flexibility in creating intricate designs and functional prototypes.
Hybrid approaches and combinations
Exploring hybrid approaches and combinations involves incorporating silicon-based materials with other printable substances to achieve the desired silicon-like properties. By blending silicon with compatible materials, you can customize the characteristics of the final printed object, balancing strength, flexibility, and conductivity.
Using hybrid approaches and combinations allows you to leverage the advantages of both silicon and other materials, unlocking a wide range of possibilities for creating complex structures with tailored functionalities.
Conclusion
Upon reflecting on the question “Can a 3D printer print Silicon?”, we have learned that while conventional 3D printers cannot print silicon due to its high melting point, special techniques such as using silicon ink can enable the printing of silicon-based structures. This advancement opens up possibilities for creating intricate silicon components for various applications in electronics, medicine, and beyond.
As technology continues to evolve, it is fascinating to see how innovations like 3D printing are pushing the boundaries of what is possible in manufacturing. So, while your standard 3D printer may not be able to print pure silicon just yet, the future holds exciting potential for advancements in this area that could revolutionize how we create complex silicon-based products.
Q: Can a 3D printer print Silicon?
A: Silicon is a challenging material to 3D print due to its high melting point and unique properties. Most conventional 3D printers are not capable of printing pure silicon. However, there are specialized industrial 3D printers that can print silicon-based materials using advanced techniques.
Q: What are the challenges in 3D printing Silicon?
A: The main challenges in 3D printing silicon include the material’s high melting point (1414°C), which exceeds the capabilities of many 3D printers. Silicon also tends to react with oxygen in the air, forming silica (SiO2), which can further complicate the printing process.
Q: Are there any alternatives to 3D printing pure Silicon?
A: While 3D printing pure silicon is difficult, there are alternative materials that can mimic some of its properties. For example, silicones and other silicon-based polymers can be 3D printed using specialized techniques. These materials offer similar flexibility and biocompatibility as silicon.