Many innovative advancements in aerospace technology are now utilizing the power of 3D printing to create complex components. From intricately designed engine parts to lightweight structural elements, 3D printing is revolutionizing the aerospace industry. In this blog post, we will explore the specific types of aerospace components that are being successfully manufactured using this cutting-edge technology, ultimately reshaping the way we think about aircraft design and production.
Key Takeaways
- Complex geometries: 3D printing allows the manufacturing of complex aerospace components with intricate designs that traditional methods cannot replicate.
- Lightweight structures: Additive manufacturing enables the creation of lightweight components, which is crucial for aerospace applications to reduce fuel consumption and increase efficiency.
- Durable materials: Aerospace components are often 3D printed using advanced materials such as titanium, aluminum, and nickel alloys to ensure strength, durability, and resistance to high temperatures and harsh environments.
Historical Background

Early adoption of 3D printing in aerospace
The aerospace industry has been an early adopter of 3D printing technology due to its ability to produce complex components with high efficiency. The technology allows for the creation of intricate designs that were previously impossible to manufacture using traditional methods. You can find a wide range of aerospace components that are now 3D printed, including engine parts, brackets, ducting, and even entire airframes.
Evolution of 3D printing technologies
Over the years, 3D printing technologies have evolved significantly, leading to improvements in speed, accuracy, and material options. Any aerospace engineer can tell you that these advancements have revolutionized the industry by enabling rapid prototyping, customized designs, and reduced costs. You will find that different types of 3D printing technologies, such as selective laser sintering (SLS), fused deposition modeling (FDM), and stereolithography (SLA), are now used in aerospace manufacturing to create a variety of components.
These technologies have made it possible to produce lightweight yet robust parts, ultimately improving the efficiency and performance of aerospace systems. You will see that 3D printing has become an integral part of aerospace manufacturing processes, offering endless possibilities for innovation and design customization.
Engine Components
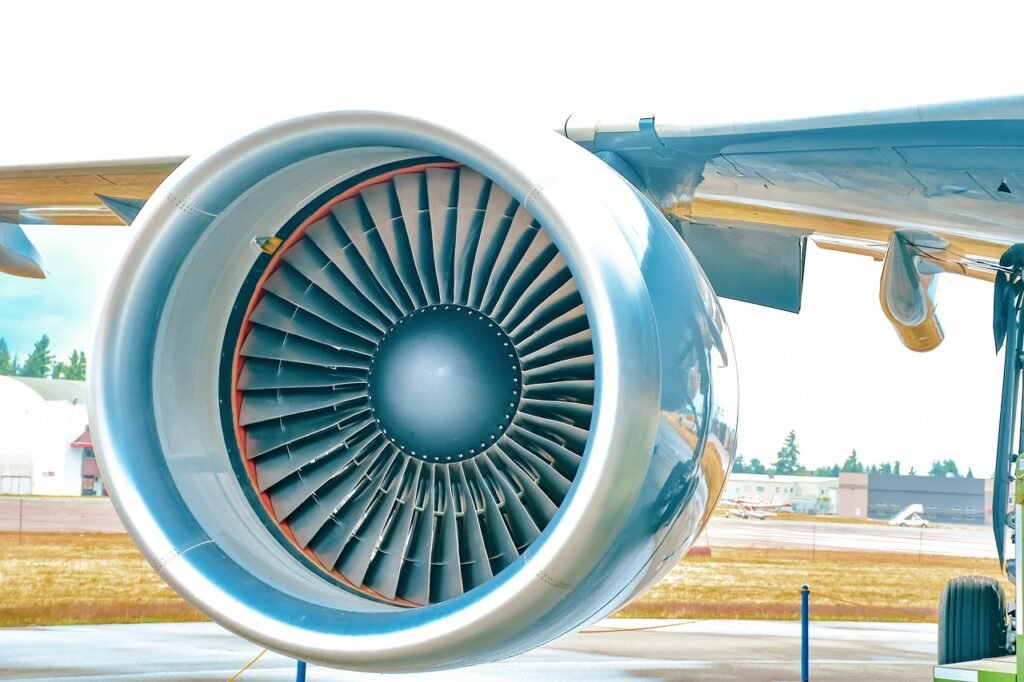
Some of the most critical components in an aircraft engine can benefit greatly from 3D printing technology. Let’s explore a few key engine components that can be produced using additive manufacturing.
Turbine blades and vanes
One area where 3D printing has made significant strides is in the production of turbine blades and vanes. These components are subjected to high temperatures and stresses, requiring intricate designs to ensure optimal performance. Additive manufacturing allows for complex geometries that are difficult or impossible to achieve using traditional manufacturing methods. This flexibility enables engineers to design more efficient and durable turbine blades, ultimately improving engine performance and fuel efficiency.
Fuel nozzles and injectors
Fuel nozzles and injectors are crucial components in the combustion process of an aircraft engine. Additive manufacturing offers the ability to create intricate internal geometries that optimize fuel atomization and combustion efficiency. For instance, GE Aviation has successfully utilized 3D printing to produce fuel nozzles with 25% fewer parts, reducing assembly time and improving overall engine reliability.
Engine mounts and brackets
With 3D printing, engine mounts and brackets can be customized to meet the specific requirements of an aircraft, providing a perfect fit and reducing weight. This customization can lead to improved structural integrity and overall performance of the engine. Additive manufacturing also allows for the production of these components using lightweight yet durable materials, enhancing fuel efficiency and reducing emissions.
Structural Components
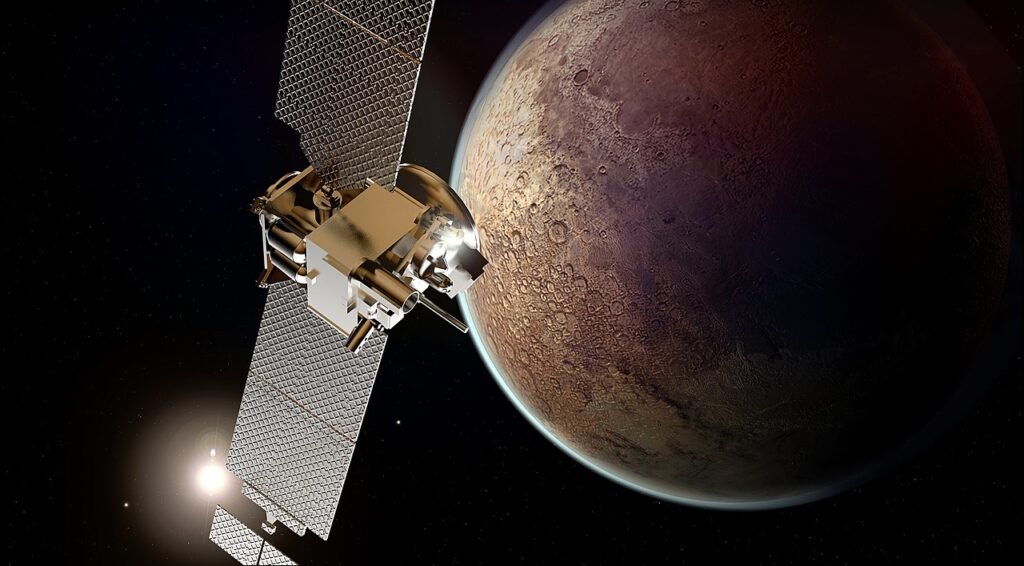
After exploring the world of aerospace components produced using 3D printing technology, let’s explore into structural components. These important parts play a crucial role in the aerospace industry, providing strength, stability, and support to various aircraft, satellites, and rockets.
Aircraft frames and fuselage parts
Aircraft frames and fuselage parts are key structural elements of an aircraft, providing the necessary framework for the aircraft’s overall structure. 3D printing has revolutionized the manufacturing of these components, allowing for complex geometries and lightweight designs that enhance fuel efficiency and overall performance. By 3D printing aircraft frames and fuselage parts, manufacturers can reduce weight, improve fuel efficiency, and streamline production processes.
Satellite components and antennas
Satellites rely on a variety of components and antennas to function effectively in space. 3D printing is utilized to manufacture these intricate parts with precision and efficiency. From satellite housings to deployable antennas, 3D printing enables the creation of lightweight yet durable components that can withstand the harsh conditions of space.
Plus, the ability to 3D print satellite components and antennas allows for rapid prototyping and customization, making it easier to adapt to specific mission requirements and optimize satellite performance.
Rocket bodies and fairings
Rockets are complex machines that require sturdy and aerodynamic components to navigate through Earth’s atmosphere and beyond. 3D printing plays a significant role in creating rocket bodies and fairings, which are important for housing the payload and ensuring a streamlined aerodynamic profile during flight.
For instance, 3D printing rocket bodies and fairings allows for the production of intricate geometries that would be difficult or impossible to achieve using traditional manufacturing methods. This capability results in lighter components, which in turn can lead to increased payload capacity and reduced costs for space missions.
Functional Components
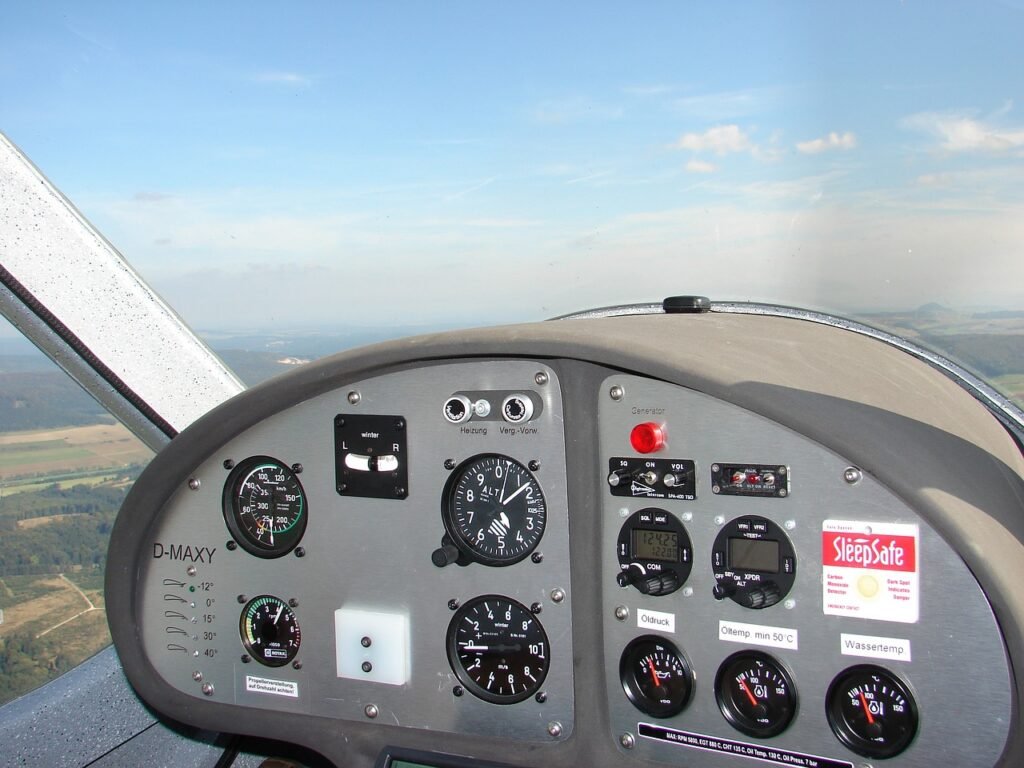
Once again, 3D printing technology has revolutionized the aerospace industry by enabling the creation of functional components that were once difficult or impossible to manufacture using traditional methods.
Hydraulic and pneumatic systems
Systems such as hydraulic and pneumatic systems play a crucial role in the functioning of aircraft, controlling various mechanisms and components. With 3D printing, complex designs for valves, manifolds, actuators, and other components can be produced with intricate internal channels and geometries that optimize performance and efficiency.
Electrical and electronic components
Components such as connectors, housings, and brackets for electrical and electronic systems in aircraft can also be 3D printed. This allows for the integration of wiring, sensors, and other electronic elements directly into the design of the component, reducing weight and improving overall system integration.
Electrical conductivity and thermal management are critical considerations for 3D printed electronic components. Specialized materials and techniques can be used to ensure that these components meet the required standards for conductivity and heat dissipation.
Thermal protection systems
Systems designed to protect aircraft from extreme temperatures during re-entry or high-speed flight can benefit greatly from 3D printing. Heat shields, ablative coatings, and insulating materials can be customized and optimized for specific areas of the aircraft, improving performance and safety.
Ablative materials can be precisely 3D printed to form intricate patterns that enhance heat dissipation and protect the underlying structure from high temperatures. This level of customization and efficiency is a game-changer for thermal protection systems in aerospace applications.
Materials Used
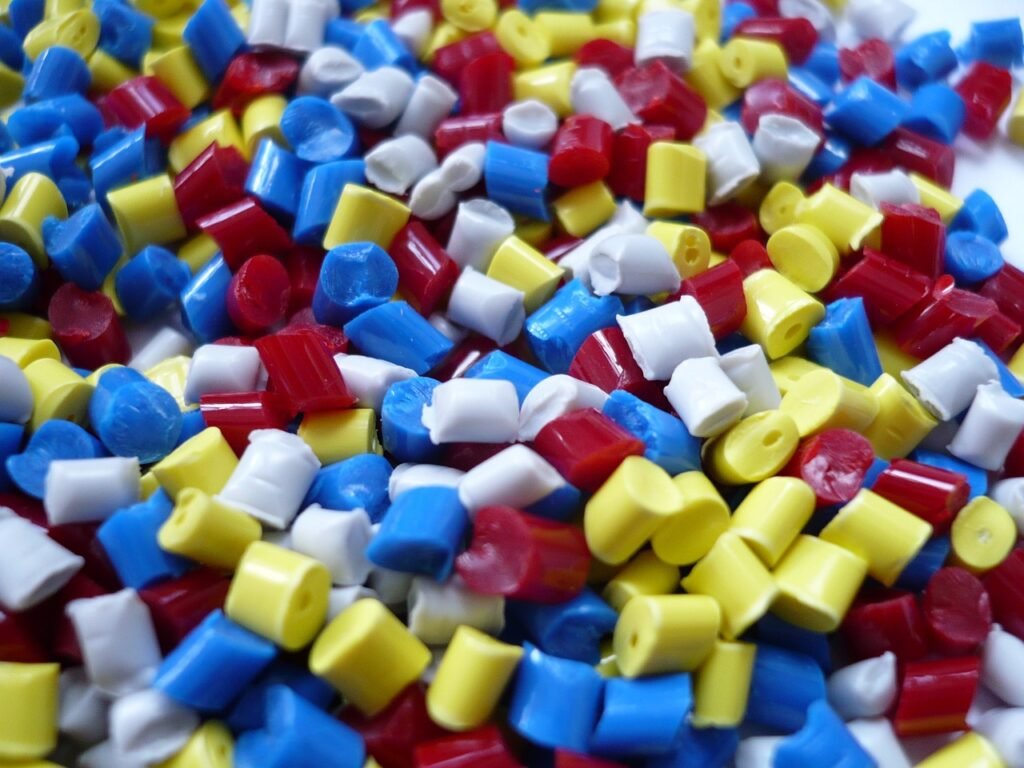
Metals (aluminum, titanium, steel)
On your journey to understanding 3D printing in aerospace, you’ll come across various materials used in the process. Metals such as aluminum, titanium, and steel are commonly utilized in the aerospace industry for their strength, durability, and heat resistance properties. These metals are crucial for creating components that can withstand the rigorous demands of aerospace applications.
Polymers (plastics, composites)
On your exploration of 3D printing materials, you’ll also encounter polymers, including plastics and composites. Polymers are lightweight materials that are ideal for creating intricate components while reducing overall weight, a critical factor in aerospace design. Composites, which combine different materials to achieve specific performance characteristics, offer a versatile solution for aerospace components.
Composites play a vital role in aerospace applications, where the need for lightweight yet strong materials is paramount. By combining different materials such as carbon fiber, fiberglass, and resin, manufacturers can create components that offer enhanced strength-to-weight ratios, improved durability, and resistance to extreme temperatures.
Ceramics and hybrids
An integral part of the 3D printing material landscape in aerospace includes ceramics and hybrids. These materials offer unique properties such as high temperature resistance, thermal insulation, and excellent mechanical strength. Ceramics and hybrid materials are often used in components that require exceptional performance in extreme conditions, making them indispensable in aerospace manufacturing.
Understanding the diverse range of materials used in 3D printing for aerospace applications is important for optimizing component design and performance. By leveraging the unique properties of metals, polymers, composites, ceramics, and hybrids, aerospace engineers can create innovative solutions that meet the stringent requirements of the industry.
Benefits and Challenges
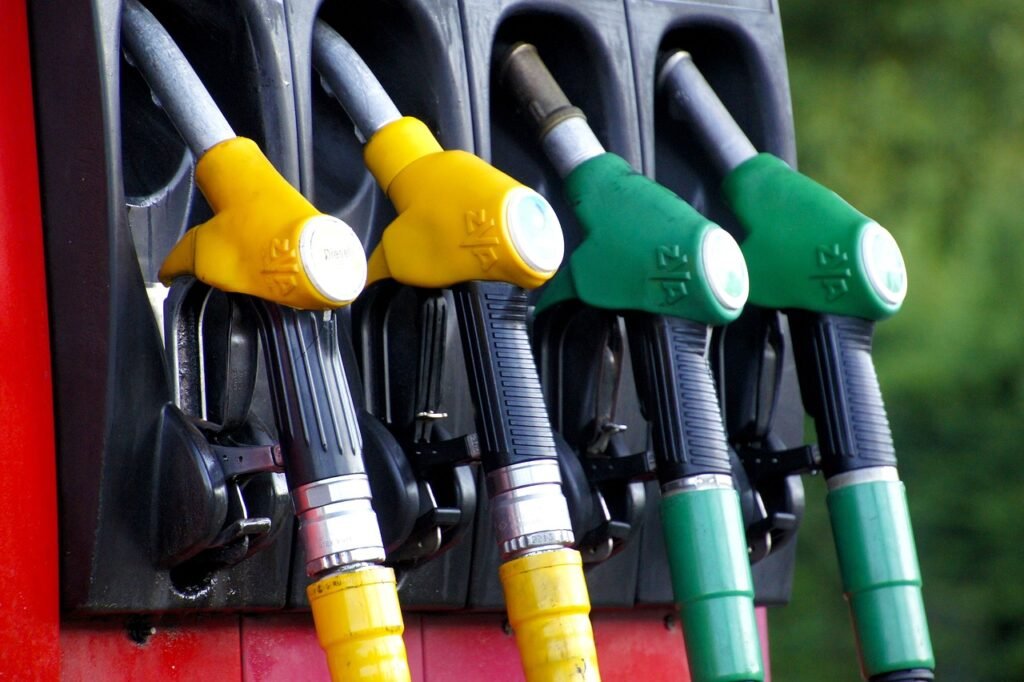
Weight reduction and fuel efficiency
With 3D printing technology, aerospace components can be designed with intricate internal geometries that reduce weight while maintaining strength. This weight reduction not only enhances the performance of the aircraft but also contributes to fuel efficiency, saving costs and reducing environmental impact.
Increased complexity and customization
Any aerospace component that requires complex geometries or customization can benefit from 3D printing. You can create intricate designs that would be impossible or extremely costly to produce using traditional manufacturing methods. This allows for unique, optimized parts tailored to your specific needs.
Another advantage of increased complexity and customization is the ability to consolidate multiple parts into a single component. By integrating functions that would traditionally require separate pieces, you can simplify assembly, reduce weight, and improve overall efficiency of the aerospace system.
Material properties and testing limitations
limitations3D printing offers a wide range of materials suitable for aerospace applications, but each material comes with its own set of properties and limitations. It’s important to understand the characteristics of the chosen material to ensure the component meets the required performance standards. Additionally, testing the 3D printed parts for reliability and durability poses a challenge, as traditional testing methods may not always be directly applicable to components manufactured using additive manufacturing techniques.
complexity3D printing technology is continually evolving to overcome these challenges, with ongoing research and development focused on improving material properties, testing techniques, and overall quality control processes. As you explore into the world of 3D printed aerospace components, remember to consider the unique characteristics and limitations of this innovative manufacturing method.
Final Words
Presently, you have gained insight into the world of 3D printing in aerospace technology. The components that are commonly 3D printed in this field include complex geometries like brackets, ducts, and heat exchangers, as well as engine parts such as turbine blades and fuel nozzles. As technology advances, the use of 3D printing in aerospace will continue to innovate and revolutionize the industry, leading to lighter, stronger, and more efficient aircraft designs. Stay tuned for more exciting developments in this cutting-edge technology!
Q: What types of aerospace components can be 3D printed?
A: Various aerospace components can be 3D printed, including complex engine parts, brackets, turbine blades, ducts, heat exchangers, lightweight structures, and even entire satellite components.
Q: How does 3D printing benefit the aerospace industry?
A: 3D printing offers numerous benefits to the aerospace industry, such as reduced weight of components, faster production times, customization capabilities, cost savings, and the ability to create intricate designs that were previously impossible using traditional manufacturing methods.
Q: Are there any limitations to 3D printing aerospace components?
A: While 3D printing has revolutionized aerospace manufacturing, it does have limitations such as material restrictions, size constraints, surface finish quality, post-processing requirements, and the need for specialized expertise to operate the technology effectively.