If you’ve ever wondered about the intricacies of 3D printing with metal, you’re in the right place. Metal 3D printing, encompassing processes like Selective Laser Melting (SLM) and Direct Metal Laser Sintering (DMLS), offers a fascinating glimpse into the world of additive manufacturing. In this article, you’ll explore the fundamental principles behind these technologies, understand their distinctive characteristics, materials used, and even investigate into the post-processing methods that elevate metal 3D printed parts to their full potential. Get ready to unravel the secrets behind this cutting-edge technology and its applications in today’s industrial landscape.
Key Takeaways
- Metal 3D printing utilizes additive manufacturing processes like SLM and DMLS to fuse metal particles together layer-by-layer, creating solid, intricate parts that traditional manufacturing methods may struggle to produce.
- The process involves spreading metal powder, scanning with a high-power laser, and repeating layer by layer until the part is complete, resulting in parts with isotropic mechanical and thermal properties, making them stronger and more flexible compared to traditionally manufactured parts.
- Materials like aluminum, stainless steel, titanium, and superalloys can be used for metal 3D printing, allowing for high-strength components with excellent properties, but post-processing steps like support removal and heat treatment are necessary to enhance mechanical properties and appearance.
What is Metal 3D Printing? The Differences Between SLM and DMLS
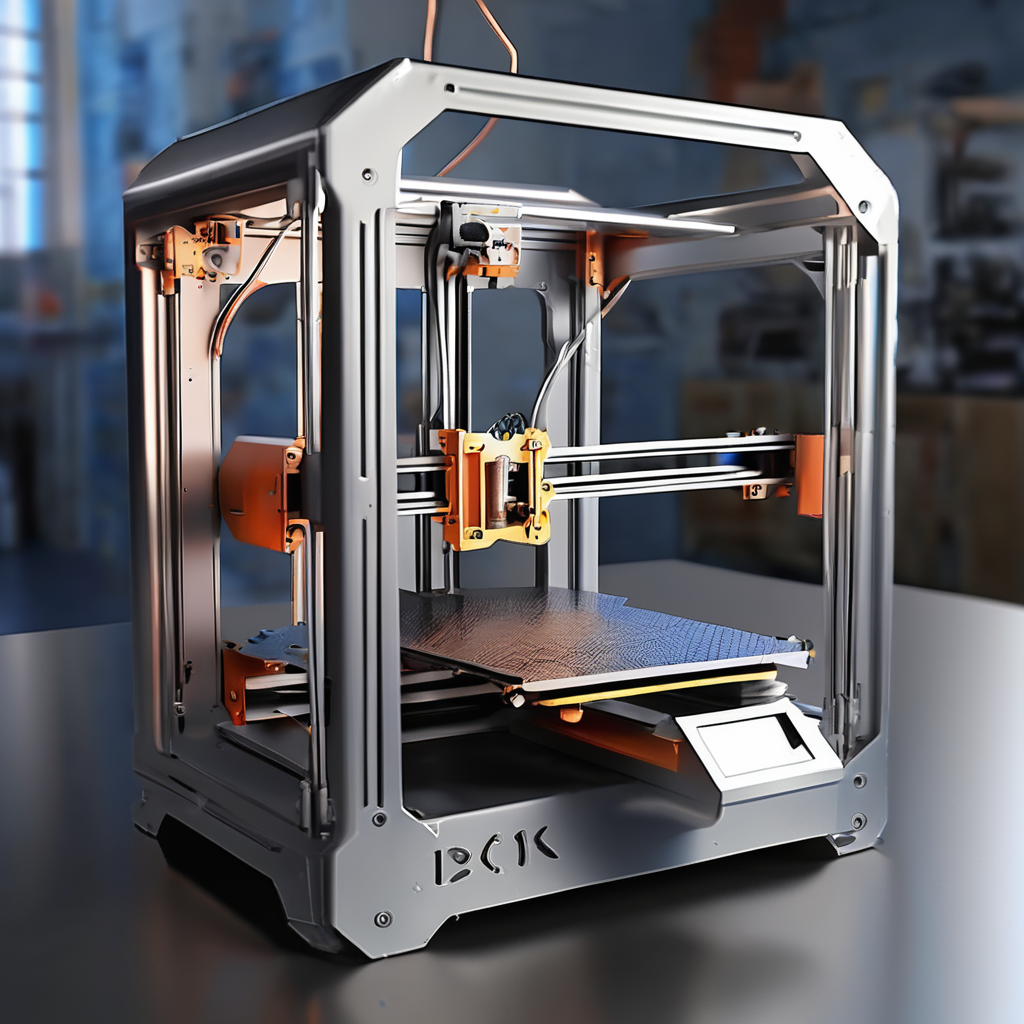
Definition of metal 3D printing
While metal 3D printing encompasses a range of additive manufacturing processes, the key methods are Selective Laser Melting (SLM) and Direct Metal Laser Sintering (DMLS). The fundamental difference lies in the way these processes bond metal particles together to create solid components.
Overview of SLM and DMLS technologies
With SLM, metal powders with a single melting point are fully melted to create parts from a single metal. On the other hand, DMLS utilizes materials with varying melting points that fuse molecularly at elevated temperatures to form metal alloys. These distinctions are crucial in understanding the capabilities of metal 3D printing.
The two technologies have a lot of similarities: both use a laser to scan and selectively fuse (or melt) the metal powder particles, bonding them together and building a part layer-by-layer. Also, the materials used in both processes are metals that come in a granular form.
How Does Metal 3D Printing Work?
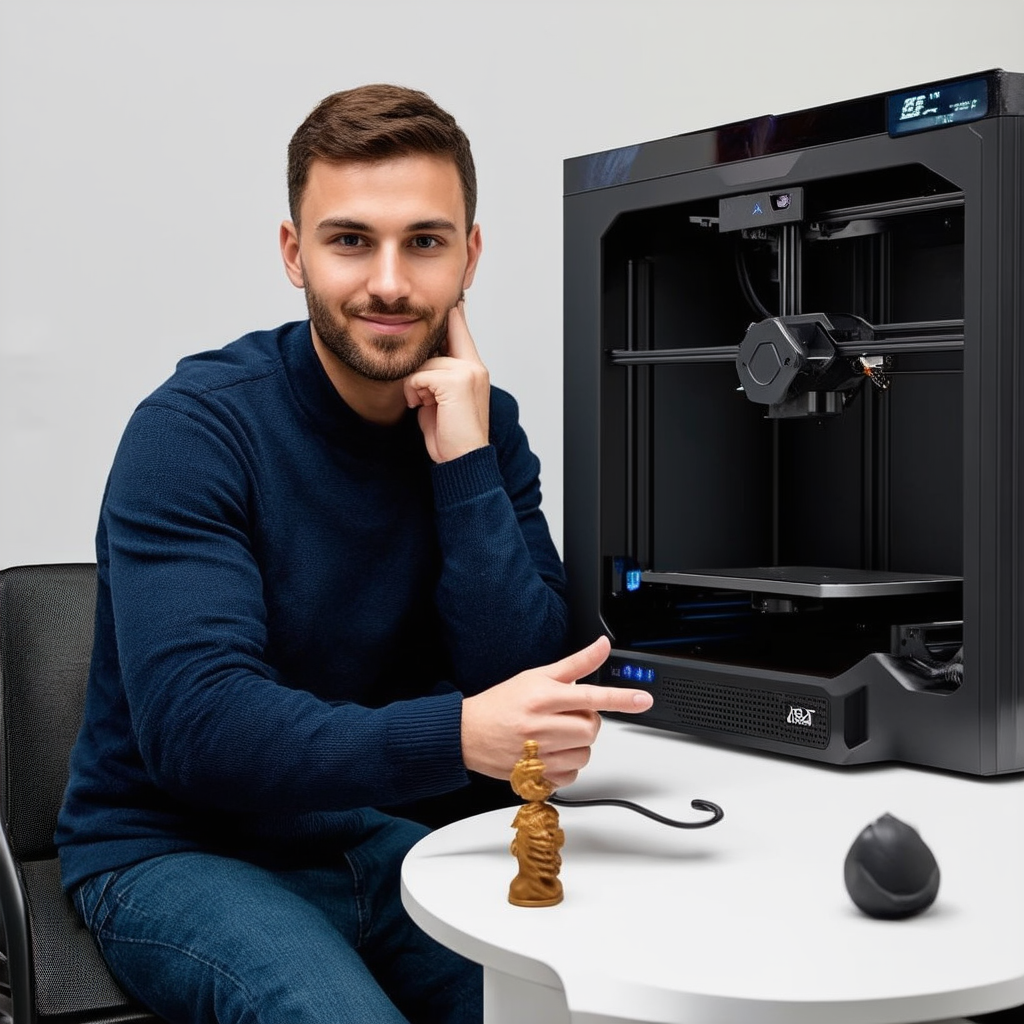
The layer-by-layer process
There’s a fascinating process behind metal 3D printing that involves building parts layer by layer. The build chamber is filled with inert gas, the metal powder is spread over the platform, and a high-power laser selectively fuses the particles together to create each layer. This layer-by-layer approach ensures precise fabrication of complex geometries.
Fusion of metal powders
Metal 3D printing involves the fusion of metal powders using a high-power laser. This process enables the metal particles to bond together, creating solid, end-use engineering products. Selective Laser Melting (SLM) fully melts the particles, while Direct Metal Laser Sintering (DMLS) fuses materials at elevated temperatures, allowing for the production of parts from metal alloys.
Furthermore, in the process of metal fusion, the as-built surface roughness of a 3D printed part is around 6 – 10 μm. This roughness can impact fatigue strength, but post-processing techniques can be employed to enhance the surface quality and mechanical properties of the final part.
What are The Characteristics of Metal 3D Printing?
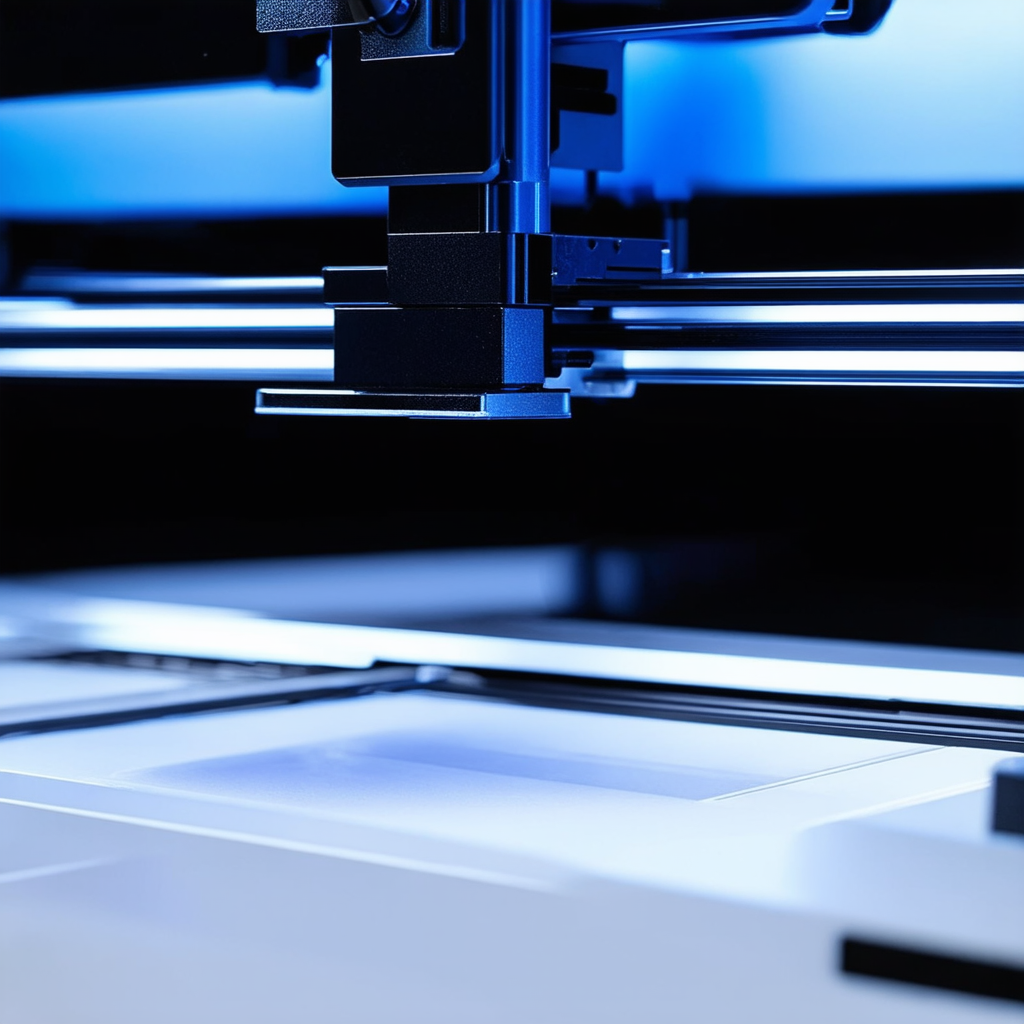
Laser power and speed
The laser power used in metal 3D printing varies depending on the material properties, typically ranging from 20 to 50 microns in layer height. The speed at which the laser scans the component is crucial in ensuring accurate fusion of the metal particles.
Build chamber atmosphere
The build chamber is filled with inert gas, such as argon, to prevent oxidation of the metal powder during the printing process. This optimizes the build temperature and ensures the quality of the final part.
Bonding mechanisms
On a molecular level, the particles in Direct Metal Laser Sintering (DMLS) bond at elevated temperatures, allowing for the fusion of materials with variable melting points. In Selective Laser Melting (SLM), particles are fully melted, creating a single metal part.
Factors affecting adhesion
Laser power, scan speed, and layer thickness all play a role in ensuring proper adhesion of metal particles. Recognizing the optimal parameters for your specific material is key to successful metal 3D printing.
- Adjusting the laser power and scan speed
- Choosing the right layer thickness
- Ensuring proper chamber atmosphere
- Selecting the correct build orientation
- Implementing effective support structures
Types of support structures
Metal 3D printing often requires lattice support structures to facilitate proper part orientation and prevent warping. Perceiving the best design for support structures can significantly impact the success of your metal printing projects.
Optimizing part orientation
For optimal part strength and minimal warping, consider orienting your metal 3D printed parts at angles that maximize support effectiveness. Optimizing the orientation of your parts during the printing process is crucial for achieving the desired results.
Design considerations
Hollow sections are not commonly used in metal printing due to challenges in support removal. However, skin and cores can be utilized to reduce print time and enhance part stability. Designing with these considerations in mind can streamline your metal 3D printing process.
Benefits of hollow sections
Metal 3D printing offers the capability to create lightweight parts with complex geometries. The ability to optimize part orientation and design for hollow sections allows you to maximize the performance of your metal printed components.
Support structures play a crucial role in metal 3D printing, ensuring the integrity of your part during the fabrication process. Perceiving the importance of these structures and designing them effectively can significantly impact the success of your metal printing projects.
What are the Common Materials for 3D Metal Printing?
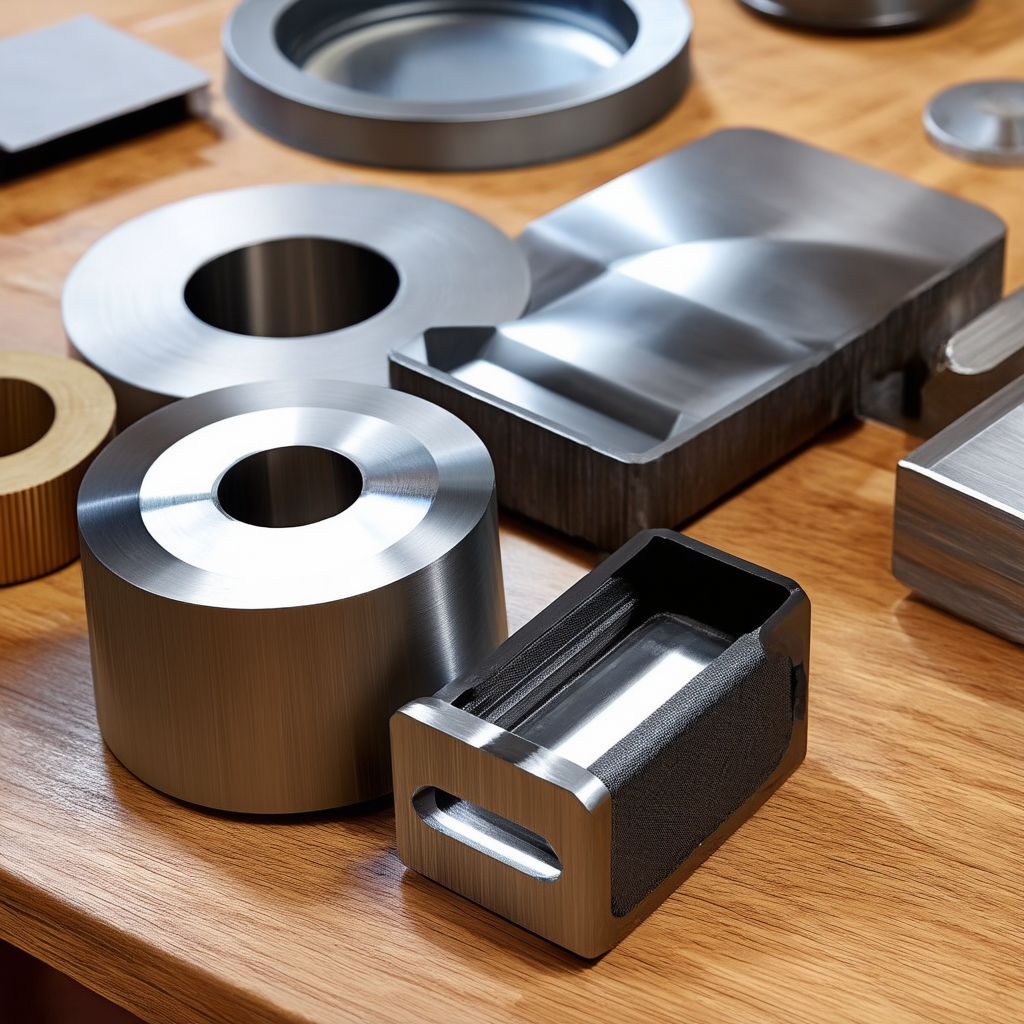
Ferrous alloys (e.g., steel, iron)
Unlike non-ferrous alloys, ferrous alloys such as steel and iron are commonly used in metal 3D printing. These materials offer good mechanical properties and thermal stability, making them suitable for a wide range of industrial applications.
Non-ferrous alloys (e.g., aluminum, copper)
Materials like aluminum and copper are popular choices in metal 3D printing due to their excellent thermal conductivity and lightweight nature. These non-ferrous alloys provide versatility in design and are often used in aerospace and automotive industries for their unique properties.
What sets non-ferrous alloys apart is their corrosion resistance and strength-to-weight ratio, which make them ideal for applications where durability and performance are necessary. Aluminum, in particular, is known for its high strength and low density, making it a preferred material for lightweight components.
Titanium and its alloys
Alloys consisting of titanium are widely utilized in metal 3D printing for their exceptional strength-to-weight ratio, corrosion resistance, and biocompatibility. Titanium parts are commonly used in aerospace, medical, and automotive industries due to their high performance and durability.
Another advantage of titanium alloys is their temperature resistance, making them suitable for applications where materials need to withstand extreme environments. Additionally, titanium parts produced through metal 3D printing exhibit superior mechanical properties compared to traditional manufacturing methods, offering enhanced performance and longevity.
Post-Processing Methods for Metal 3D Printing
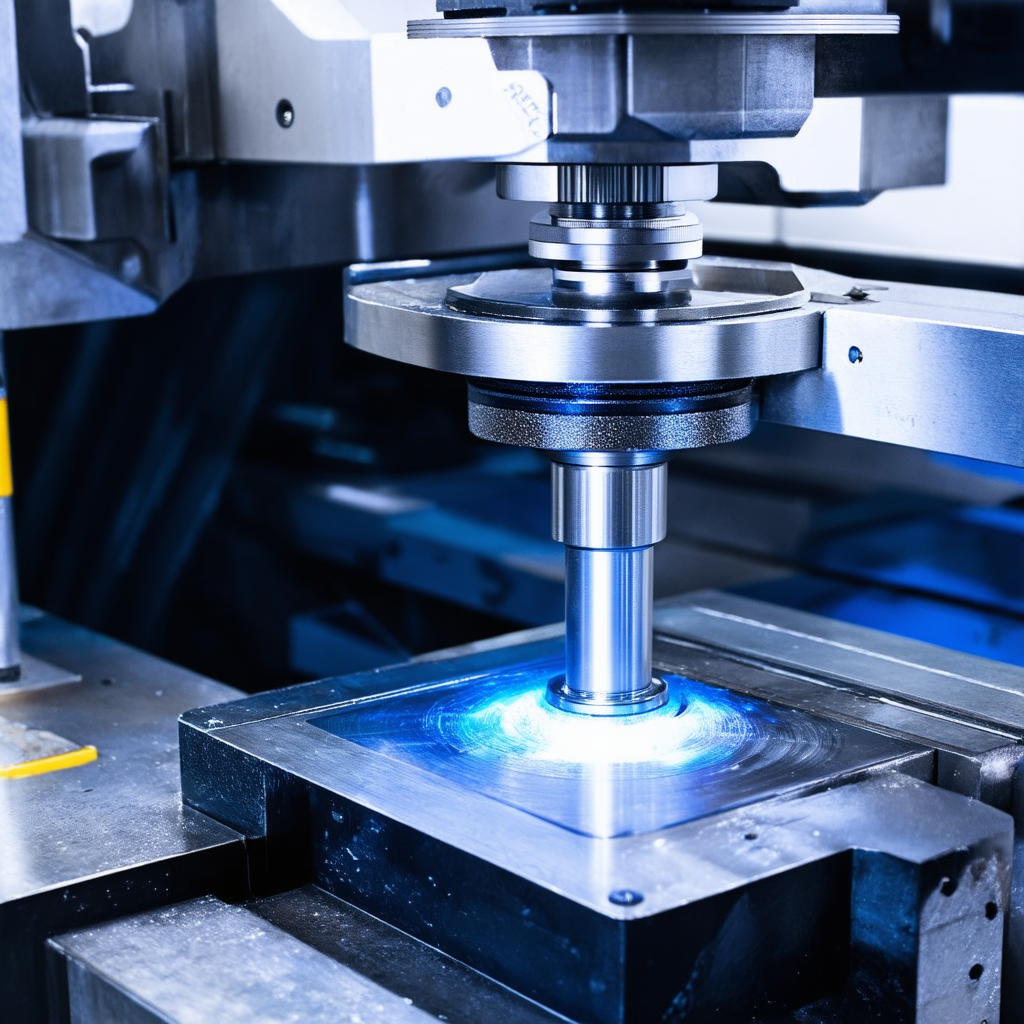
Machining and grinding
An vital post-processing step for metal 3D printed parts is machining and grinding. This involves using CNC machining to ensure dimensionally crucial features like holes or threads are accurate and to refine the surface finish of the part. By employing these techniques, you can enhance the overall precision and quality of your metal printed components.
Heat treatment and annealing
After printing, heat treatment and annealing are commonly used post-processing methods for metal 3D printed parts. Heat treatment helps to relieve residual stresses and improve the mechanical properties of the component. The annealing process involves subjecting the part to specific temperatures for a set period, enhancing its strength and durability.
Surface finishing techniques
The final stage in post-processing metal 3D printed parts involves surface finishing techniques. This may include media blasting, metal plating, polishing, and micro-machining. These techniques serve to improve the appearance, texture, and fatigue strength of the metal printed components, ensuring they meet the desired specifications and aesthetics.
What are the Benefits & Limitations of Metal 3D Printing?
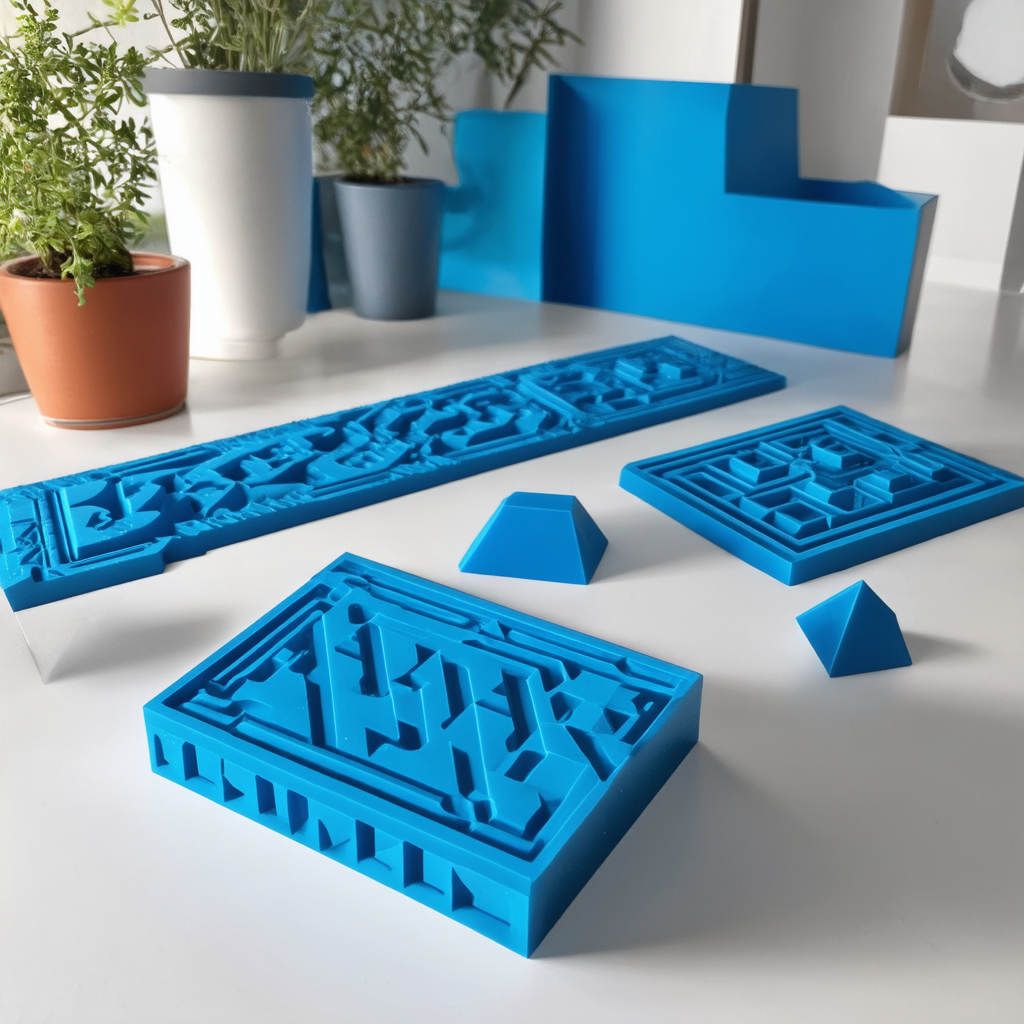
Advantages: complex geometries, reduced material waste
The benefits of metal 3D printing are significant. Despite the high costs, this technology allows you to manufacture complex, bespoke parts with geometries that traditional methods cannot achieve. Topologically optimized metal parts ensure maximum performance while minimizing weight and reducing material waste. The available range of materials includes challenging-to-process metal superalloys, offering excellent physical properties for your products.
Limitations: high cost, limited material options
For all its advantages, metal 3D printing does have some limitations. The high material and manufacturing costs associated with this technology mean it may not be suitable for easily producible parts. Additionally, the limited build size of metal 3D printers restricts the size of components that can be created. Existing designs may require modification to be compatible with metal 3D printing methods.
Plus, the range of available materials for metal 3D printing, while diverse, can be restricted in comparison to traditional manufacturing methods. Precious metals, for example, are mainly used in jewelry making and may not be widely available for other applications.
Conclusion
When exploring metal 3D printing, it’s important to consider a range of factors such as design complexity, material selection, and cost implications. You have learned about metal 3D printing, specifically the processes of Selective Laser Melting and Direct Metal Laser Sintering. You now understand how these additive technologies work, from the layer-by-layer fabrication process to the post-processing methods used to enhance the mechanical properties of metal printed parts. By understanding the benefits and limitations of metal additive manufacturing, you can make informed decisions regarding its application in your projects. Keep exploring and designing, as the possibilities with metal 3D printing are endless!
FAQ
Q: What is metal 3D printing?
A: Metal 3D printing is an additive manufacturing process that utilizes metal powders to create three-dimensional objects layer by layer. This technology allows for the production of complex and customized metal parts that traditional manufacturing methods may struggle to achieve.
Q: How does metal 3D printing work?
A: Metal 3D printing, specifically through processes like Selective Laser Melting (SLM) and Direct Metal Laser Sintering (DMLS), involves using a high-power laser to selectively fuse metal powder particles together, building the desired part layer by layer. This bonding process results in strong, solid metal components with intricate geometries.
Q: What are the benefits of metal 3D printing?
A: Metal 3D printing offers the advantages of creating complex, bespoke parts, topologically optimizing designs for maximum performance, and utilizing a range of materials, including challenging superalloys. It opens up new possibilities for manufacturing high-quality metal components that may not be achievable through traditional methods.
Q: What are the limitations of metal 3D printing?
A: While metal 3D printing is a cutting-edge technology, it comes with limitations such as high material and manufacturing costs, restricted build sizes due to precise control requirements, and the need for design modifications to adapt existing models for additive manufacturing. Understanding these limitations is crucial for effective utilization of the technology.
Q: What materials can be used for metal 3D printing?
A: A variety of materials can be utilized for metal 3D printing, including aluminum alloys, stainless steel, titanium alloys, cobalt-chrome superalloys, and nickel superalloys like Inconel. Each material offers unique properties suited for different applications, expanding the possibilities for metal additive manufacturing.